Local Services
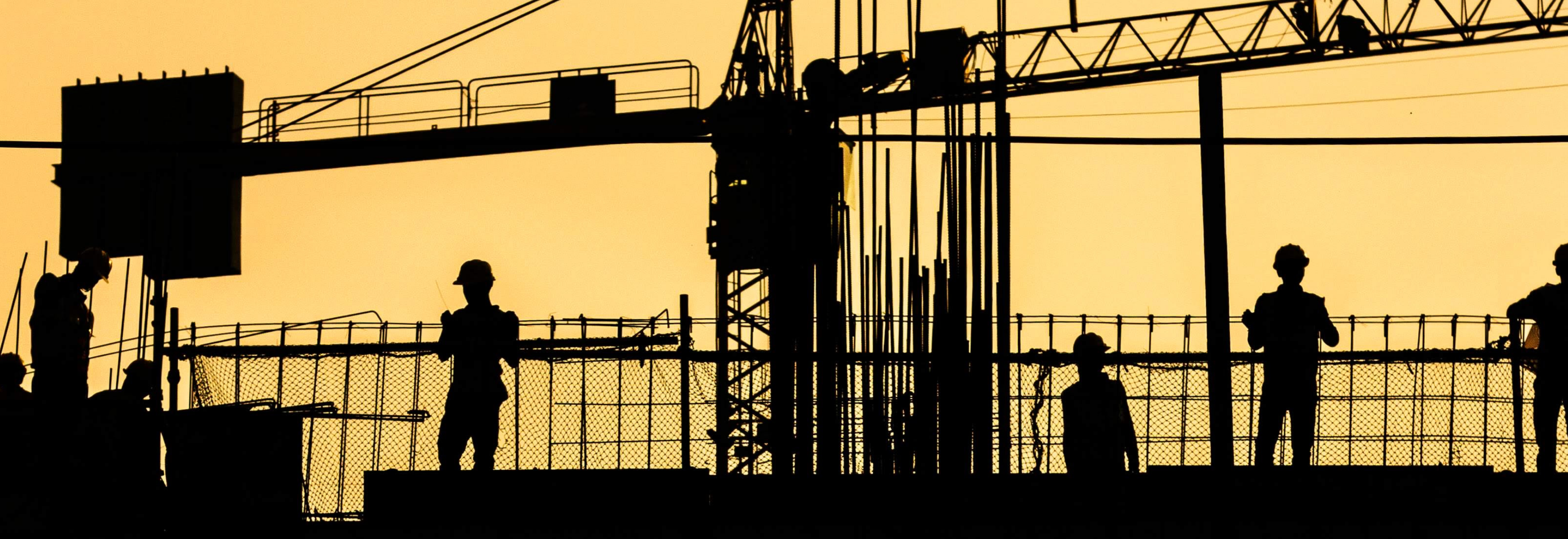
Key Services in Philippines
Established in 1989, Mitsubishi Power (Philippines) Inc., houses the only Boiler Manufacturing Plant in the Philippines. Over the years, we have built unique capabilities and technologies for complex on-site construction services.
Beyond this, optimum power plant performance and giving our customers peace of mind are top priorities. We uphold stringent project control ensures that on-site installation and repairs are done safely, efficiently and affordably. Our services include O&M, inspection, long-term service agreements for power plants, training, and remote monitoring.
After Sales Service
Our engineers are committed to ensuring the safety and durability of power generation equipment throughout their lifespans. We leverage cutting-edge technology for plant diagnosis, refurbishment consultation, O&M, revamps and upgrade services to improve plant availability.
-
Plant Maintenance and Rehabilitation We pride ourselves in providing cost-effective solutions for complex and urgent on-site repair, modification and maintenance of boilers and their related plant parts, while adhering to stringent safety measures.
-
Thermal Spraying
Thermal spraying is a surface modification technology using electrical energy or combustion flame to melt a surface to produce a film coating on a wide variety of materials (metal, ceramic, cermet, plastic) and is used in various industrial fields including boiler furnaces and turbines for protection against wear and tear as well as corrosion.
We apply various techniques of thermal spraying on boiler panels to prevent plant faults arising from the thinning of boiler tubes for stable plant operation. These include Arc Spraying and High Velocity Oxygen Fuel (HVOF) for local application. A combination of spraying techniques can also be used according to specific plant part requirements.
-
Faro 3D Scanning
We utilize FARO 3D scanners which are small and lightweight, with extra-long range and extended scanning possibilities even in direct sunlight as well as easy positioning with the integrated GPS receiver. It utilizes a contactless measurement system to scan wide areas such as plant topography, large structures and parts at high speed while recording three-dimensional coordinate data.
-
Drone Technology
We leverage drone technology for assessment of equipment within 30 minutes. This also helps our engineers to improve boiler inspection procedure and capabilities.
Damaged tubes and leakage points inside the boiler can be located and documented without the use of any scaffoldings, which minimizes shutdown duration of power plants for maintenance.
Boiler Assets Services And Assessment Technologies
We house the only boiler manufacturing plant in the country which manufactures power boilers, industrial boilers, conventional boilers, circulating fluidized boilers and heat recovery steam generators.
Our expertise with the design, manufacturing, operation, and maintenance of boilers allows us to offer the most cost-effective approach to improve plant availability.
-
Risk-based Maintenance
We offer Risk-Based Maintenance (RBM) to assess equipment risk according to the likelihood of damage and the potential impact of equipment fault which may be calculated in terms of financial loss, repair costs, human injury, and environmental damage.
Benefits of RBM:
• Prioritize urgent maintenance
• Lower maintenance costs
• Improve plant availability
• Accurate estimation of remaining lifespan -
Ultrasonic Thickness (UT) Mapping
Ultrasonic Testing (UT) Mapping is a testing technique that assesses boiler damage for necessary maintenance like thermal spray application as well as aid in further study to improve boiler operation.This allows our engineers to monitor damage status to prevent tube failure while spares parts are prepared for replacement. -
Cableless Inner UT System
We leverage a cableless inner UT system which uses a small ultrasonic sensor that moves along the boiler tube with the use of water pressure. The system is capable of measuring tube thickness over the whole circumference and its full length.As a result, 90% of the system’s total weight is reduced in comparison with the conventional system which requires a large signal cable feeding device and pressure pump.
TOMONI HUB (Analytics and Performance Center)
We house a TOMONI HUB in Alabang, Philippines, one of five facilities globally and the only one in APAC. TOMONI HUBs provide real-time, cyber-secure interactive support of plant operation and maintenance decision making.
With data, we deliver early warnings and detection of anomalies or needed corrective action to avoid unit trips or load reductions, help diagnose performance loss and design plans to optimize plant operations. This helps to eliminate energy efficiency losses and avoid unnecessary maintenance.
Boiler Manufacturing Capabilities
A pioneer in design and manufacturing of power boilers and industrial boilers in the country, our production capability boasts 450 tons/month, equivalent to five boiler units for a 150 MW plant per year for boiler pressure parts.
We produce sub-critical to supercritical pressure parts including water wall tubes, screen tubes, superheaters, economizers, reheaters, drums, headers and other pressure vessels as well as non-pressure parts and piping components of power boilers.
Quality Assurance
We maintain the most exacting standards in our manufacturing processes. Our equipment is made from top-grade materials that pass rigorous control checks and significant testing.
In production processes, we implement the Quality Management System (QMS) in accordance with ISO 9001:2015. To compliment and support the QMS, several quality processes have also been established which meet the requirements of internationally recognized codes and standards such as American Society of Mechanical Engineers, Ministry of Economy, Trade and Industry and Japanese Industrial Standards.