News
Integrated solution for sewage sludge mono-combustion
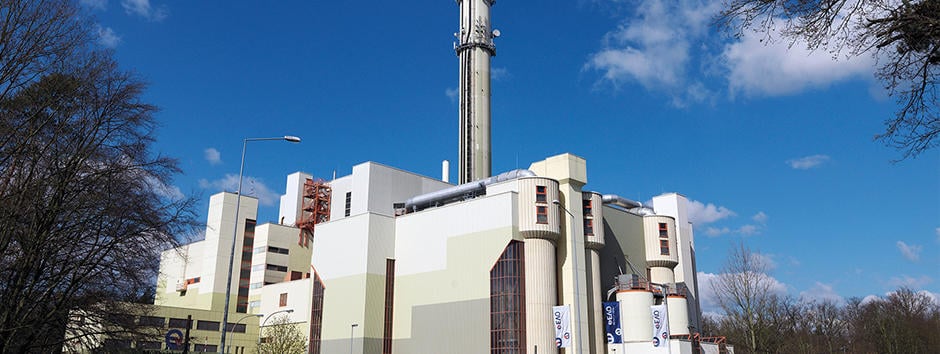
In Offenbach, Mitsubishi Power is currently building an integrated solution for sewage sludge mono-combustion with a rotary kiln system at the Waste to Energy plant there. The plant, built in 1995, consists of three lines with roller grate firing and handles annually 300,000 tons of waste, incl. 20,000 tons sewage sludge as secondary fuel. The WtE plant is being extended by a 2-line rotary kiln system which will be connected to two of the three WtE boilers. The total annual volume of the plant will thus be increased to a maximum of 300,000 t/a waste and 100,000 t/a sewage sludge. In addition to the rotary kilns, the heart of the Mitsubishi Power system is a combination of mill, post-combustion chamber and cyclone. The flue gas required for the operation of the rotary kiln system and for the ash post-combustion is taken from two of the existing boilers. The sewage sludge ash produced in the rotary kiln is first milled in the downstream process, then fed to the hot gas stream of the post-combustion chamber and finally separated from the flue gas in a cyclone. In addition to this process, the design of the rotary kilns is being optimized (modified blades in the drying area, diverter blocks in the burnout zone, rotation of the gas stream).
Europe’s Most Innovative Waste-to-Energy Project
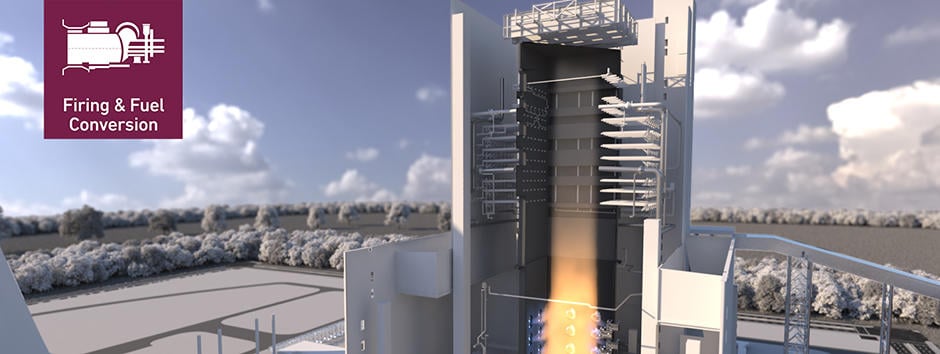
The “Uskmouth Conversion Project” in the UK is the first example of such scale where a previously coal-fired station successfully tested to run on waste-derived fuel pellets. Mitsubishi Power has completed the largest ever combustion testing of the fuel pellets at Uskmouth. The pellets are composed of about 50% plastic waste and 50% material such as paper, cardboard and wood, to be used as new fuel at the plant. The converted station is expected to consume around 900,000 metric tons of waste pellets every year. Mitsubishi Power DS® Ultra-Low NOx Burners used at the station are able to combust the waste-derived fuel without gas or oil support firing, allowing to operate continuously at 25 MW thermal power. During the testing it was concluded that it was possible to feed large volumes of pulverized fuel into the burner via a pneumatic system without disturbances. Flue gas emissions were within anticipated levels and the burner was able to achieve expected low NOx performance while maintaining low CO levels. The technologies implemented in this project will open up new markets globally for future similar conversions. Generating sustainable energy is one of Mitsubishi Power’s key goals and missions for the coming future.
Modernization of two Combustion boilers including the grate system for Waste Incineration plant Spittelau
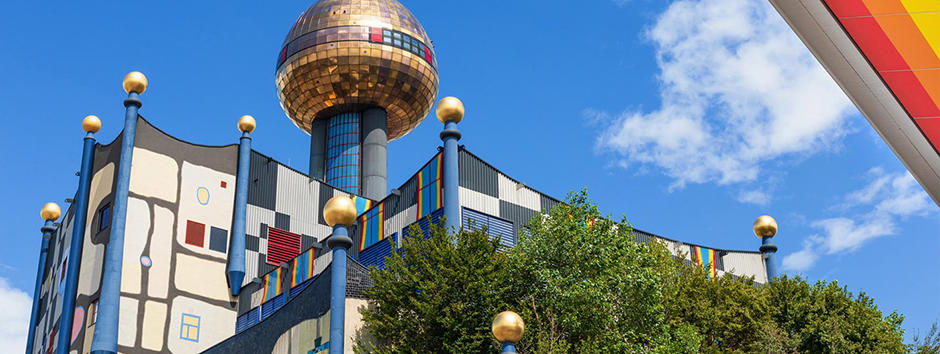
For Wien Energy GmbH, Mitsubishi Power modernized one of the most impressive Waste to Energy plants in Austria. Two combustion boilers including the moving grate systems of the Plant designed by the artist Hundertwasser were fully renewed in 2014/2015. The impact of the modernisation was three-fold. While heat extraction remains stable, the plant’s power generation capacity has trebled. The new denitrification system cut down consumption of natural gas by about 5 million m3 annually. Lower pollution levels have translated to a more positive impact on the community. Spittelau has among the best emission levels in Europe, while also setting a new international standard.
The complete scope of service was the engineering, delivery, installation and commissioning of:
- Combustion boiler
- Moving grate system
- Combustion air system
- Fabric filter
- Boiler and boiler house steel structure
- Ash and slag removal system
- Activated carbon ash dosing plant
- Cooling water plant
- Nitrogen (Inert-) System
- Insulation of Boiler
- Balance of Plant
Fuel | Waste |
---|---|
Net calorific value | 10 MJ/kg |
Waste feed rate | 2 x 16 t/h |
Boiler capacity | 2 x 55 t/h |
Operating pressure | 40 bar |
Steam temperature | 400°C |