Delivery Case Examples
Fabric Filter for Coal Fired Boilers
For pulverized coal fired boilers
This is an example of application in exhaust gas treatment of a pulverized coal fired boiler. We reduced the installation area of the fabric filter by setting the filter cloth length to 9 m compared to the normal filter cloth lengths of 6.0 m and 6.9 m. By applying a long filter cloth to a fabric filter with a large capacity for gas treatment, it is possible to reduce the size of the system. We reduced the pressure loss during operation with the adoption of the new venturi, and reduced the power consumption of the blower.
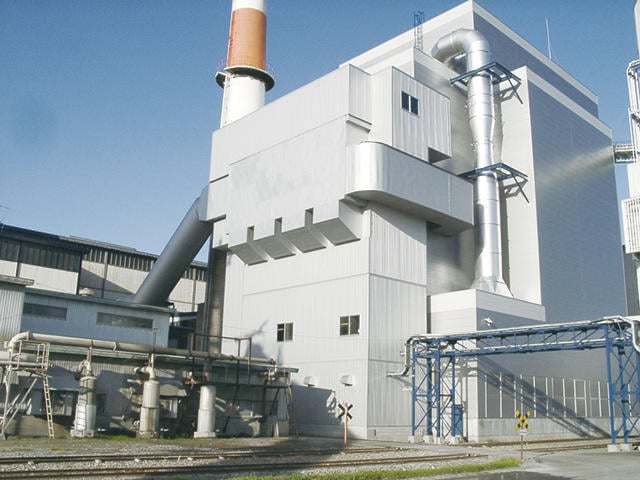
Process flow
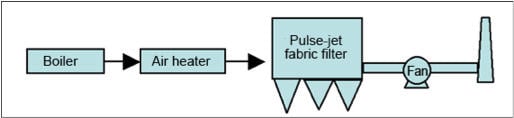
Fabric Filter for Steel Manufacturing Industry
(1) For coke oven gas
It is an example where fine dust is collected by suctioning the coke oven gas. We reduced the pressure loss of the fabric filter by adding a coarse-particle auxiliary agent, and thereby achieved energy-saving operation.
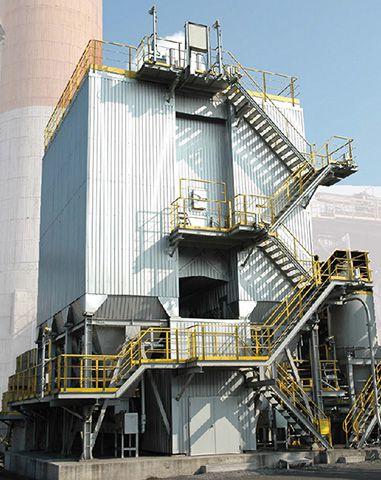
Process flow
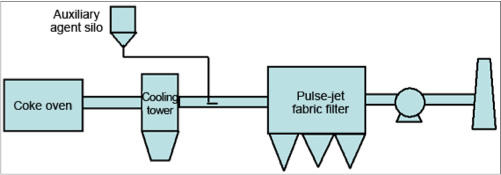
(2) For cutting slabs
This is an example where dust in exhaust gas from a stainless steel slab cutting machine is collected. By charging the fine stainless steel particles generated by gas cutting and agglomerating them at the static electricity charged section, the collection performance of submicron particles is improved. In addition, it results in energy saving as it reduces the pressure loss of the fabric filter. This type of fabric filter which has a static electricity charged section in the process preceding the fabric filter is called an electrostatic fabric filter.
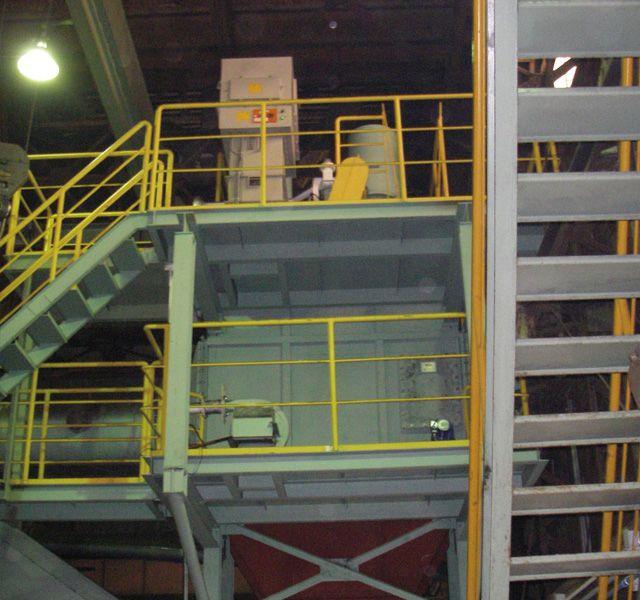
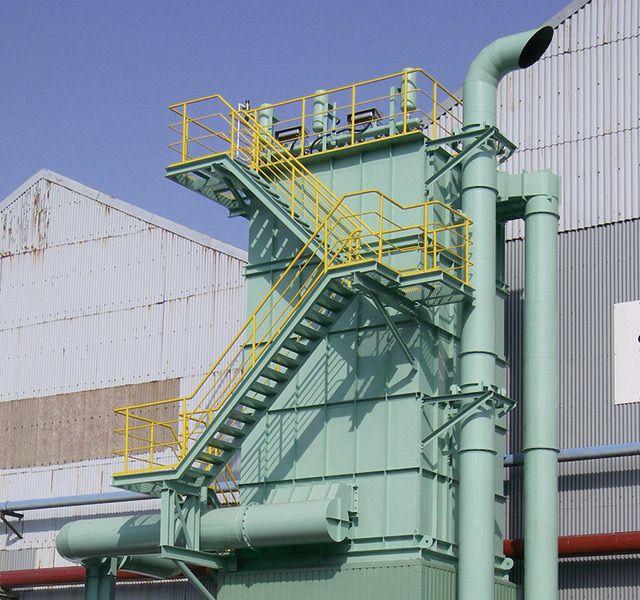
Process flow
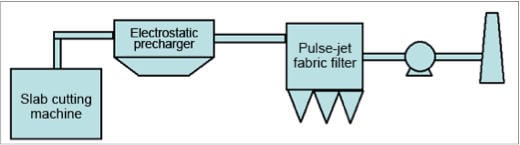
Fabric Filter for Cement Industry
For cement firing equipment
This is an example of application in exhaust gas treatment of a cement firing furnace and suspension preheater. The exhaust gas from the cement firing furnace is led to the fabric filter after removing the coarse particles with the cyclone preduster. This gas contains fine, highly concentrated cement dust, which is collected by the fabric filter. The fabric filter is divided into multiple dust collection chambers, and the gas flow in the dust collection chambers is sequentially stopped to dispel the collected dust using a pulse jet. By dispelling with a pulse jet using the airflow shielding (off-line method), stable operation can be achieved with reduced pressure loss. The collected cement dust is reused as raw material for cement.
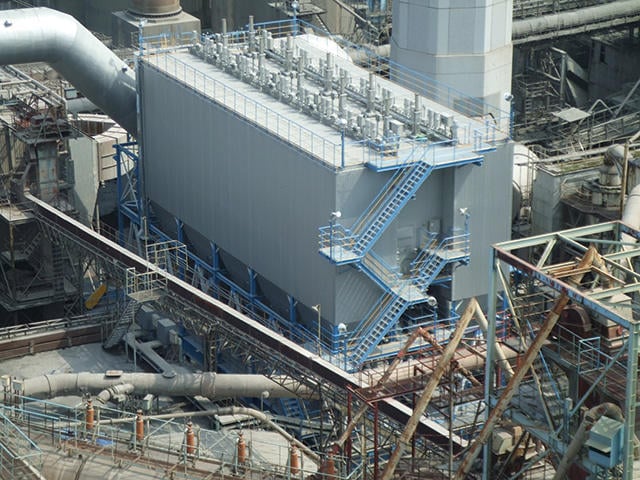
Process flow
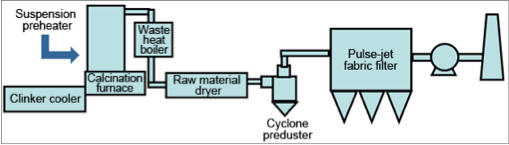
Fabric Filter for Waste Incinerators
For waste incinerators
This is an example of treating the waste incinerator exhaust gas using a filter cloth added with a dioxin decomposition catalyst (catalyst carrying filter cloth). It decomposes and removes the trace amounts of gaseous dioxins contained in exhaust gas from waste incinerators and removes dust with high performance.
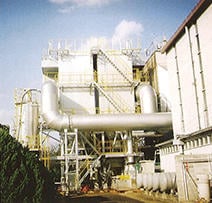
(outdoor installation)

(indoor installation)
Process flow
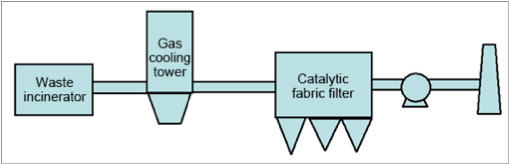