(Energy Conservation I) Steam Conservation Adaptive to Operating Conditions
Effective Resources Utilization
Summarized proposition
The solvent recovery equipment employs a variety of automatic energy-saving systems adaptive to operating conditions. It carries out from uniform continuous desorption as required on maximum load to intermittent desorption associated with load changes to minimum steam consumption. The resultant ratio of steam consumption in the pattern illustrated below will equal T1/T2.
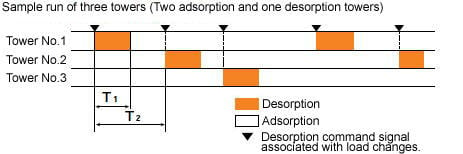
Sample run of three towers (Two adsorption and one desorption towers)
System Outline
Exhaust Gas Concentration System
As shown in the lower right diagram, the solvent reaches a breakthrough state as the adsorption capacity gets saturated.
Hence, the correct exhaust concentration of each adsorption tower is detected by the concentration detector as in the upper right diagram to launch an automatic transition from adsorption to desorption, thereby assuring maximum activated charcoal adsorption utilization to reduce the number of runs of desorption/adsorption required to a minimum.
The exhaust gas concentration system not only saves steam requirements but also greatly aids as a pollution control facility in detecting failures in their early stages of occurrence and checking activated carbon performance.
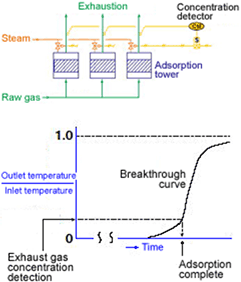
Raw Gas Load Counter System
Where multiple gas sources exist, the raw gas load counter system counts the load at the inlet of the recovery equipment from signals representative of their respective operating conditions and switches from adsorption to desorption automatically when the inlet load reaches the maximum adsorption load for one tower.
The number of runs of desorption/adsorption required is thus always kept minimal as with the exhaust gas concentration detection system. Signals (pulses) proportionate to varying gas sources are transmitted to ensure that the raw gas loads will be counted as correctly as possible.
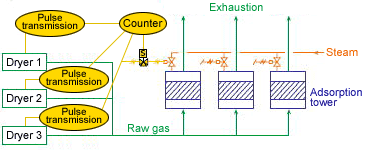
Raw Gas Concentration System
The raw gas concentration system detects the concentration and flowrate of the solvent generated and counts the volume of the solvent at the inlet of the recovery, switching from adsorption to desorption automatically when the inlet volume reaches the maximum adsorption load for one tower.
The number of runs of desorption/adsorption required is thus always kept minimal.
The system is characterized by its ability to determine the inlet loads correctly even where loads arising from a single source or multiple sources vary widely or frequently.
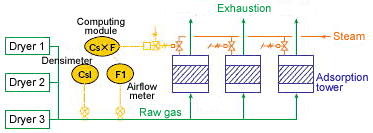
- (Energy Conservation I) Steam Conservation Adaptive to Operating Conditions
- (Energy Conservation II) Power Conservation Adaptive to Operating Conditions
- (Energy Conservation III) Exhaust Heat Recovery Adaptive to Usage Goals Effective Resources Utilization
- Offensive Odor and VOC (Volatile Organic Compounds) Control
Services
- Electrostatic Precipitator
- Fabric Filter
- Water Treatment & Sludge Treatment
- Limestone-gypsum Desulfurization System
-
Organic Solvent Exhaust Gas Treatment System
- (Energy Conservation I) Steam Conservation Adaptive to Operating Conditions
- (Energy Conservation II) Power Conservation Adaptive to Operating Conditions
- (Energy Conservation III) Exhaust Heat Recovery Adaptive to Usage Goals Effective Resources Utilization
- Offensive Odor and VOC (Volatile Organic Compounds) Control