Membrane Bioreactor (MBR) Technology
Membrane Bioreactor Method
The introduction of membrane separation technology has become a viable option for sewage and domestic wastewater treatment thanks to the recent decrease in membrane costs. MF membranes for membrane bioreactor (MBR), such as polyethylene hollow fiber membranes and polyolefin flat membranes were developed in the 1990s, and this led to the establishment of an innovative method to filter through highly concentrated activated sludge.
The Immersion Type Membrane Separation System (Mitsubishi Membrane Bioreactor System or MMBS) adopts a type of MBR that uses MF membranes, and it offers many advantages such as cost reduction effects through reduction of sedimentation ponds, sand filtration facilities, etc., and reduction of the land area, as well as ensuring high quality treated water.
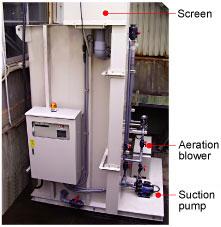
Main features of MBR and comparison with conventional methods
Small installation area
No sedimentation equipment is required as it is solid-liquid separation with a membrane.
The compact biological reaction tank maintains a high concentration and it eliminates the need for sludge concentration facilities by ensuring that the extracted sludge is high concentration.
No need for sludge concentration facilities
Due to the high concentration of mixed liquor suspended solids (MLSS) in the biological reaction tank (8,000 to 15,000 mg/L), it is possible to conduct the dehydration process on the extracted sludge as it is.
Easy operation management
It requires fewer daily management items, and there is no need to control the sedimentation of the sludge.
Extremely high water quality
Clear treated water is obtained since it applies solid-liquid separation with a membrane.
Resistant to changes in the load of sewage that flows in
There is little impact of deterioration in sludge properties related to sedimentation such as bulking because it applies solid/liquid separation with a membrane.
Ideal for recycling systems
Water can be recycled, including flushed water from toilets and water for other miscellaneous purposes, after simple sterilization.
Recycling of water for advanced requirements such as make-up water for boilers is also possible by combining it with an RO membrane.
Basic flow
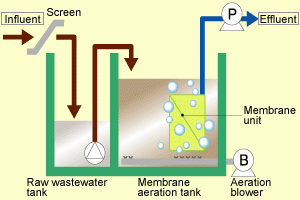
Processing regions and applications of various filtration membranes
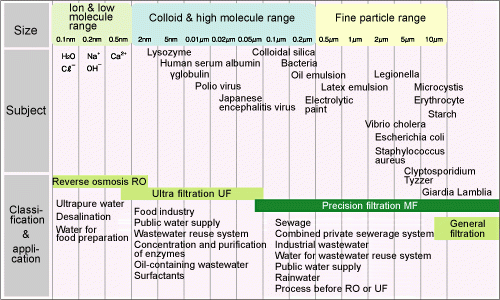
Thickness of a human hair: 120 μm to 150 μm
Case examples of wastewater treatment water quality
Item | Combined septic tank | Wastewater from pastry production | Livestock wastewater | ||||
---|---|---|---|---|---|---|---|
Raw water | Setting value | Measured value | Raw water | Treated water | Raw water | Treated water | |
pH (mg/l) | 5.8~8.6 | 5.8~8.6 | 7 | 4 | 7 | 7.6 | 6.3 |
BOD (mg/l) |
200 | ≦5 | 0.5 | 2,000 | 3 | 18,000 | 2 |
COD (mg/l) | 150 | ≦10 | 5 | 600 | 12 | 4,800 | 130 |
SS (mg/l) | 250 | ≦5 | < 1 | 1,500 | < 1 | 12,000 | < 1 |
T-N (mg/l) | 50 | ≦10 | < 6 | 50 | 1 | 3,100 | 60 |
T-P (mg/l) | 5 | ≦0.5 | < 0.5 | 20 | 1 | 370 | 120 |
Item | Microbrewery wastewater | Dairy industry wastewater | ||
---|---|---|---|---|
Raw water | Treated water | Raw water | Treated water | |
pH (mg/l) | 6 | 7.4 | 6.6 | 7.6 |
BOD (mg/l) | 1,000 | 5.4 | 1,100 | 2.7 |
COD (mg/l) | 460 | 30 | 280 | 8 |
SS (mg/l) | 69 | < 1 | 170 | 1.6 |
T-N (mg/l) | 42 | 34 | 65 | 2 |
T-P (mg/l) | 21 | 20 | 9.4 | 0.5 |