(Energy Conservation II) Power Conservation Adaptive to Operating Conditions
Effective Resources Utilization
Summarized proposition
The solvent recovery equipment implements an array of energy-saving systems adaptive to the operating conditions. The equipment is also run to follow raw gas flow changes to minimize power consumption.
It allows the airflow in a fixed suction tank to be normally reduced easily to about one half, since lower activated charcoal passage wind velocities do not adversely affect performance.
Please note, however, that excessively reduced airflow could keep the activated charcoal layer underdried and otherwise adversely affect wind velocity distributions, resulting in degraded performance.
As airflow is reduced, the airflow resistance in the system diminishes, so that the power will fall theoretically in proportion to the cube of the flowrate. The power also varies significantly depending on the flowrate reduction mechanism.
Outline of the System
Lower Vane Control System
The lower vane control system controls the blower suction port vane to follow the ON/OFF or airflow reduction status of the source and adapt to the optimal suction airflow at all times. This results in a by far more cut in power requirements than reducing the airflow with a regular damper.
While the vane control signal is collectable from the operating conditions on the source side, the standard practice is to allow the system to keep the static pressure in the raw gas duct constant.
An atmospheric air suction system is in combined use to assure minimum flow, thereby preventing performance from being degraded by overreduced airflow and offering enhanced safety (against ketonic solvents).
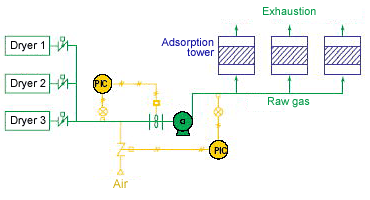
Blower Revolution Control System
The most effective way to cut power requirements is by implementing blower revolution control.
Generally, this method should prove economical when used in high-capacity tasks or in situations where low-load operations up to 70 percent or so are dominant.
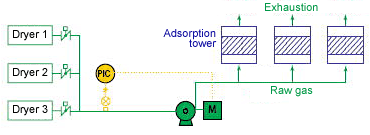
- (Energy Conservation I) Steam Conservation Adaptive to Operating Conditions
- (Energy Conservation II) Power Conservation Adaptive to Operating Conditions
- (Energy Conservation III) Exhaust Heat Recovery Adaptive to Usage Goals Effective Resources Utilization
- Offensive Odor and VOC (Volatile Organic Compounds) Control
Services
- Electrostatic Precipitator
- Fabric Filter
- Water Treatment & Sludge Treatment
- Limestone-gypsum Desulfurization System
-
Organic Solvent Exhaust Gas Treatment System
- (Energy Conservation I) Steam Conservation Adaptive to Operating Conditions
- (Energy Conservation II) Power Conservation Adaptive to Operating Conditions
- (Energy Conservation III) Exhaust Heat Recovery Adaptive to Usage Goals Effective Resources Utilization
- Offensive Odor and VOC (Volatile Organic Compounds) Control