ARTICLE
Celebrating National Manufacturing Day at Mitsubishi Power
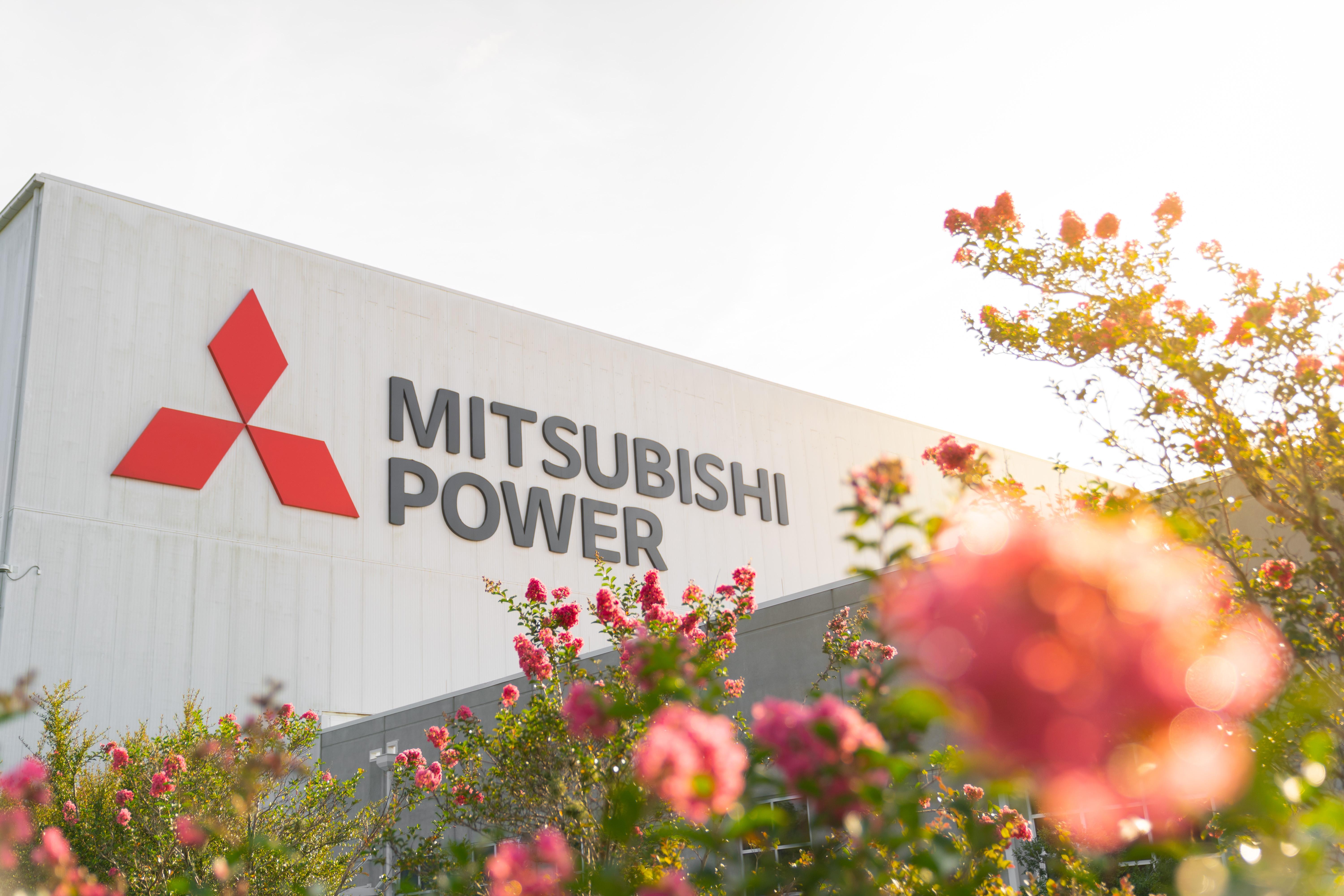
Forging a Brighter Future
“Everyone needs power, everyone needs light. Energy generation manufacturing is a great opportunity to be part of something that truly makes an impact,” says Michael Suarez, our Vice President of North American Manufacturing. In the heart of the American energy landscape, where innovation and industry converge, Mitsubishi Power stands as a beacon of progress.
Over the years, our company has been reshaping the way the world harnesses energy. But what truly sets us apart is our unwavering commitment to American manufacturing and the dedicated team that drives our success. From our state-of-the-art facilities to the skilled individuals behind the scenes, Mitsubishi Power is more than just a name; it’s a testament to the power of American ingenuity.
At Mitsubishi Power, we’re proud to be at the forefront of that impact, continually pushing the boundaries of what’s possible in energy generation. The Energy Transition might be driven by the market, but it is paved by people.
More Than Just Metal: A Conversation with the Makers
To truly grasp the impact of Mitsubishi Power’s operations, we listen to the voices behind the machinery. Their stories vividly illustrate the passion and purpose driving Mitsubishi Power’s success.
Meet Mike
In his own words, Michael Suarez was “born and raised in Mitsubishi.” As you step into the Orlando Service Center lobby, a bright room with high ceilings and a spacious layout decorated with a unique blend of traditional Japanese decor and industrial American manufacturing, you’re welcomed by people like Mike. He begins, “If you’re a good leader, you can connect with your people. You can build relationships, and they trust you and want to work with you. If you can’t establish trust, you’re going to fail.”

This philosophy of trust and relationships is a foundation for everything Mitsubishi Power North American Manufacturing does. Suarez himself has had a front-row seat to this commitment, starting as an intern in 2007 while attending the University of Central Florida. His journey of almost 20 years with the company brings him to where he sits today – as the Vice President of North American Manufacturing at the Orlando Service Center. One of the many philosophies that Mitsubishi Power embraces from its Japanese heritage is the commitment to investing in people and their abilities, rather than simply filling roles when vacancies occur.
“I had a technical degree,” Suarez muses. “My transition into a leader happened naturally when my mentor, Bob Provitola, insisted I take a step out of my comfort zone to become a supervisor. I learned that anyone could learn the technical aspect of the job, but leadership is a talent.” The lesson isn’t lost on Suarez, who reflects: “he recognized the leadership potential in me.” Today, Suarez continues this legacy at Mitsubishi Power by mentoring others in the same way.
Meet Katlyn
While leadership certainly is a talent that comes naturally to others, it is sometimes also a role assumed by those who rise to it indirectly. Katlyn Lewis’s leadership falls into the latter category.
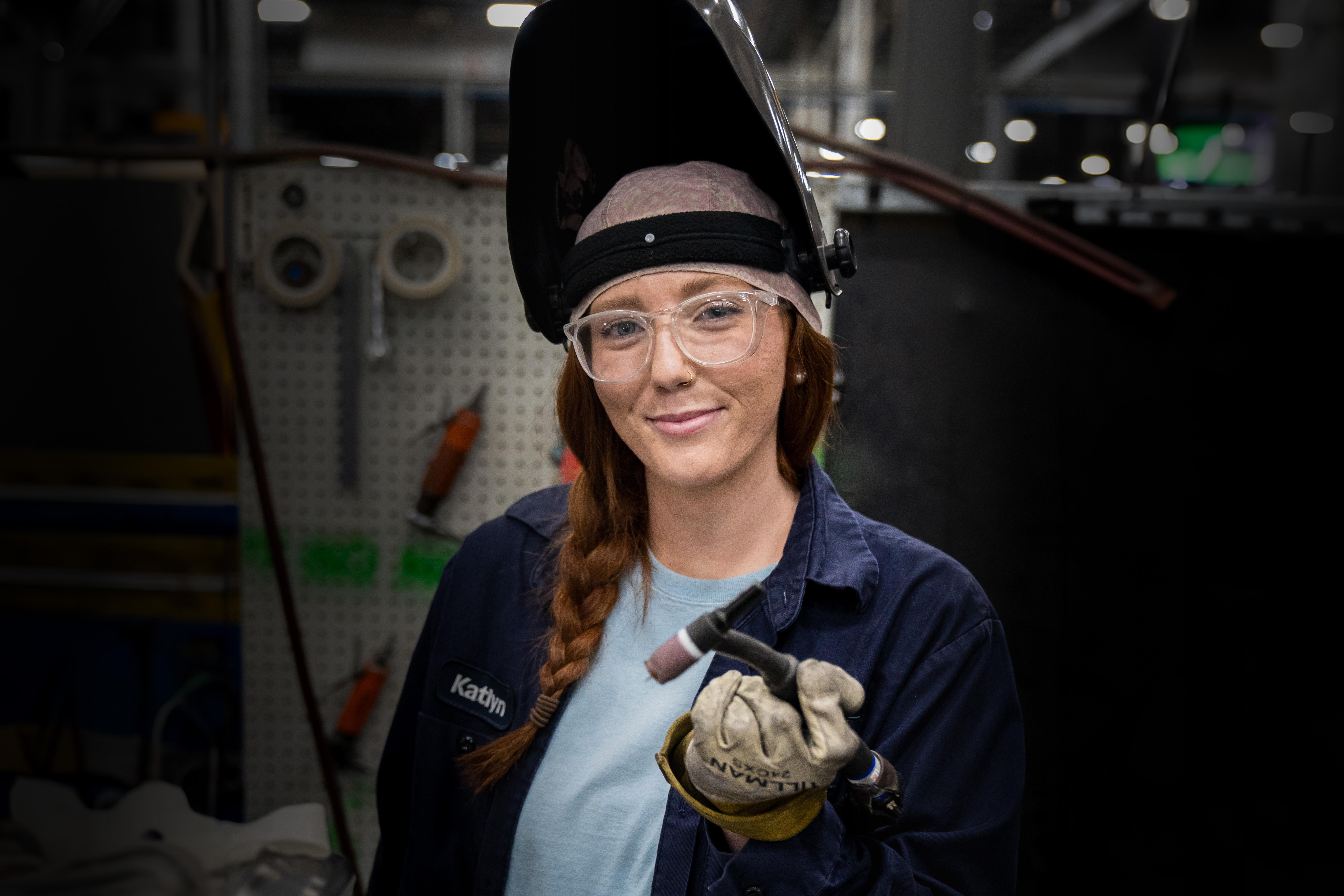
With a disarming smile, Lewis confidently embraces her role as a welder. Though manufacturing is undoubtedly a male-dominated field, Lewis has found her footing – and a support system – through her coworkers.
Lewis recognizes that “as a society, we often hear of negative experiences and hardships that women face in a male-dominated workforce.” These experiences are sometimes more noticeable in labor-intensive and skill-based settings like welding. In the Mitsubishi Power Manufacturing family, however, those experiences for Lewis have been in the minority. “While everyday tasks are not always a breeze, I know I have coworkers that never hesitate to help or lend a hand when I need it,” she says.
Lewis’s passion for welding started as a student in trade school. Her position as a welder in our Savannah Machinery Works facility allows her to professionally pursue that passion and expand her knowledge. As she continues to develop her skills and take on new challenges, Lewis is not just shaping her future but also contributing to the innovative landscape of the industry.
Meet Joe
Co-worker support and a strong sense of family are the cornerstones of our manufacturing facilities. Joe Venckauskas, Director of Operations for Component Repair and New Manufacture described employee appreciation as “the most rewarding project” he has undertaken during his tenure. “We win or lose as a team,” Venckauskas noted. “When the whole team is held accountable for issues or successes, it engages everyone to have the same mindset and same drive.”
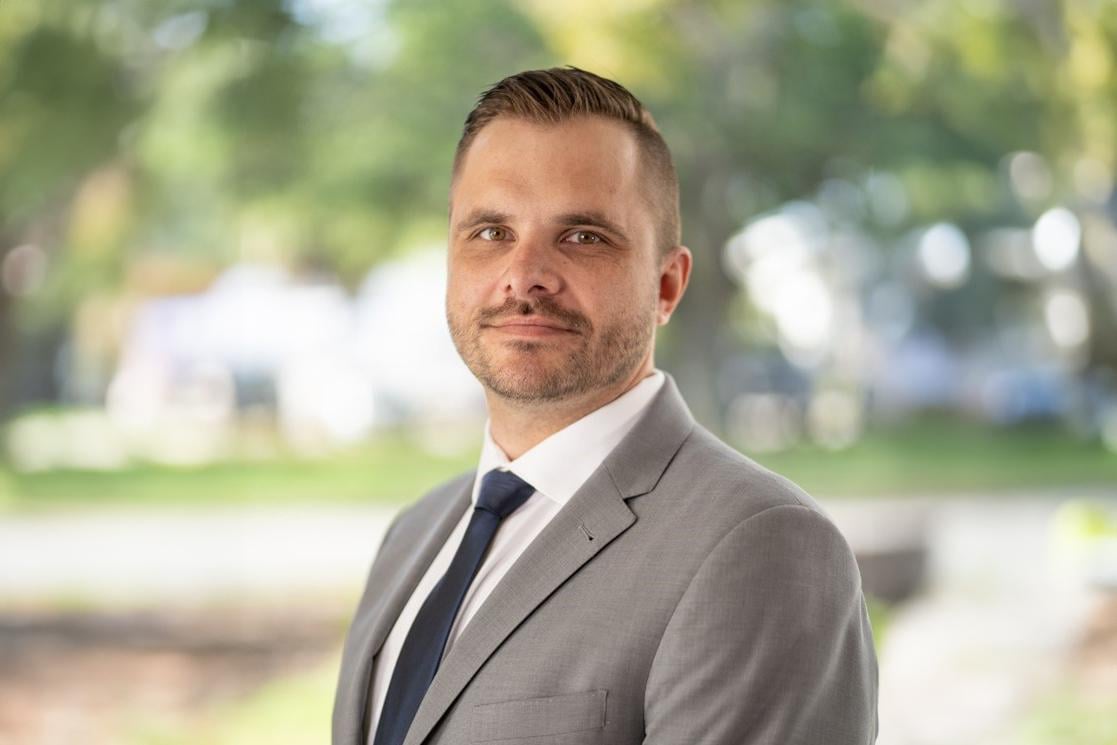
Venckauskas, who is approaching nearly a decade with Mitsubishi Power, keeps the culture top of mind in his day-to-day interactions as he oversees repairs and manufacturing operations. In fact, he starts each day with a team meeting. The team conducts a walkthrough of the production floor to review safety, quality, delivery, and productivity issues from the previous day. This meeting not only prepares each team for the day ahead but also helps identify incremental areas for improvement. This emphasis on identifying incremental areas for improvement reflects another key Japanese philosophy.
Kaizen is the commitment to continuous improvement. Distinctly different from finding fault with existing processes or people, kaizen is the philosophy of embracing the forward-facing and recursive nature of human learning and applying this to all areas of life – office included.
“We work in a very specialized manufacturing environment, so we try to build and grow from within as much as possible. Many of our supervisors started out on the floor as hourly workers and have ascended through the ranks to lead shifts or departments,” Venckauskas said. This demonstrates the intense intrinsic value of tribal knowledge that exists in the North American Manufacturing teams. Who better to lead than those who have direct insight and understanding in the day-to-day function of manufacturing?
A Legacy of Innovation: Mitsubishi Power's Journey
Spotlight on Growth and Demand in North American Manufacturing
Each of these employees provide a spotlight on some of the hidden corners of North American Manufacturing. Stories like these – ones that are unique, insightful, and powerful – demonstrate Mitsubishi Power at our best. We have come a long way from our humble beginnings in a Nagasaki dockyard nearly 200 years ago, and there are no signs of slowing down anytime soon.
“We repair 14,000 parts and make about 5,000 parts each year, and we’re still growing.” Suarez says. “There’s a high demand for reliable backup power sources with data centers for AI coming online and increased use of renewable energy. We’ve grown almost 50% since 2021 and I expect the growth to continue through 2028 because of the market.”
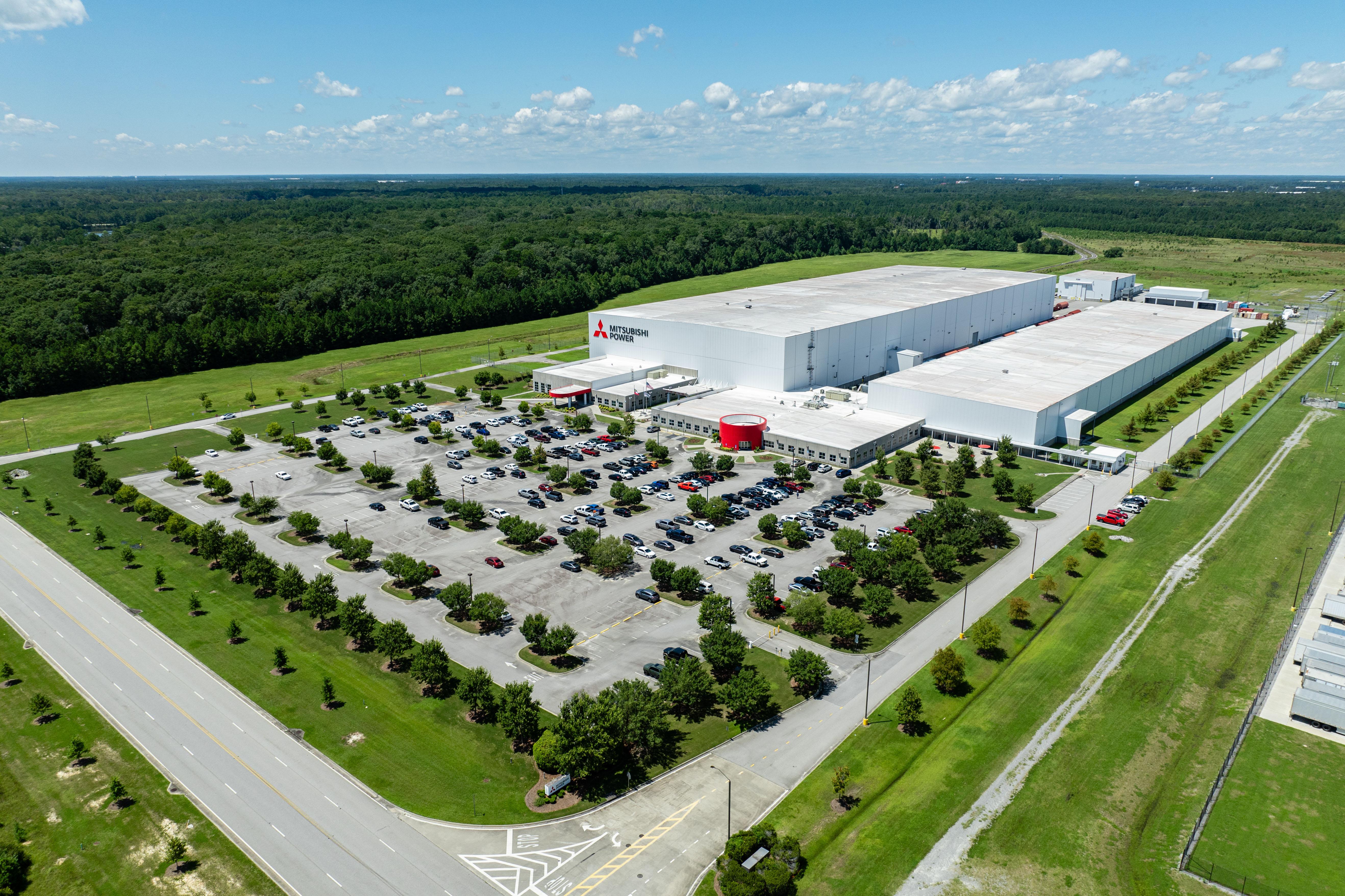
[Above: Savannah Machinery Works]
Commitment to Advanced Technology
For decades, Mitsubishi Power has delivered advanced technology in power generation to support, shape, and accelerate the energy transition. In the past 10 years alone, Mitsubishi Power has committed more than $600 million of capital investment toward new North American service and manufacturing facilities — the most significant capital investment made by any turbine manufacturer in that timeframe.
Suarez explains, Energy generation manufacturing is a great opportunity to be part of something that really makes an impact. It doesn’t take a degree. With the right motivation and attitude, the opportunities are endless.”
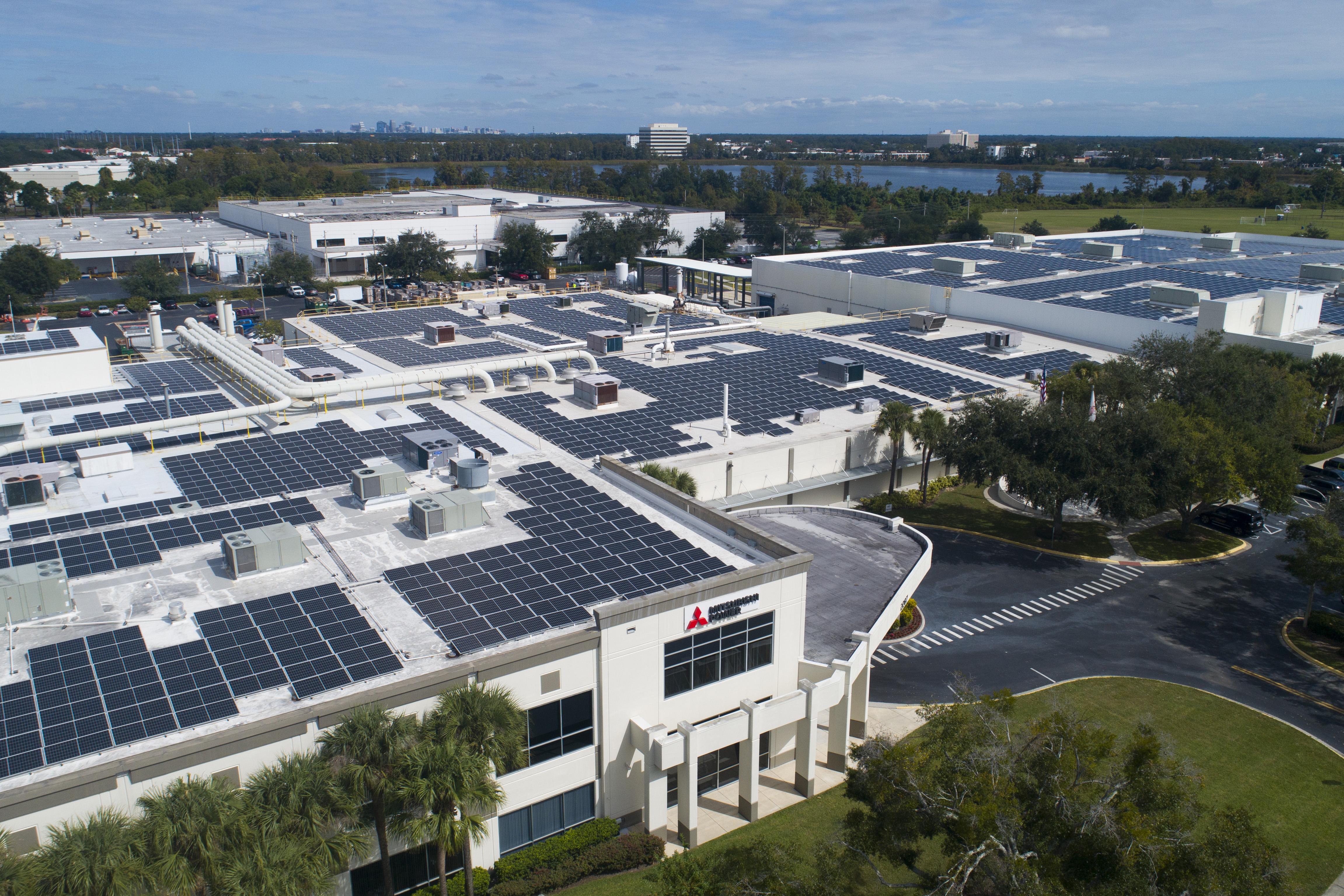
[Above: Orlando Service Center]
Our Manufacturing Facilities, Orlando & Savannah
The Orlando Services Center, which began operations in 2001, was a strategic expansion to enhance Mitsubishi Power’s manufacturing capabilities and support its power generation business in North America. The facility houses state-of-the-art machinery and technology for the precision assembly and testing of gas turbines, steam turbines, and other power generation components. Following suit nine years later, Mitsubishi Power opened the Savannah Machinery Works in Pooler, Georgia, investing over $300 million to build one of the largest facilities to manufacture, test, and service the gas and steam turbines essential for North America’s growing energy needs.
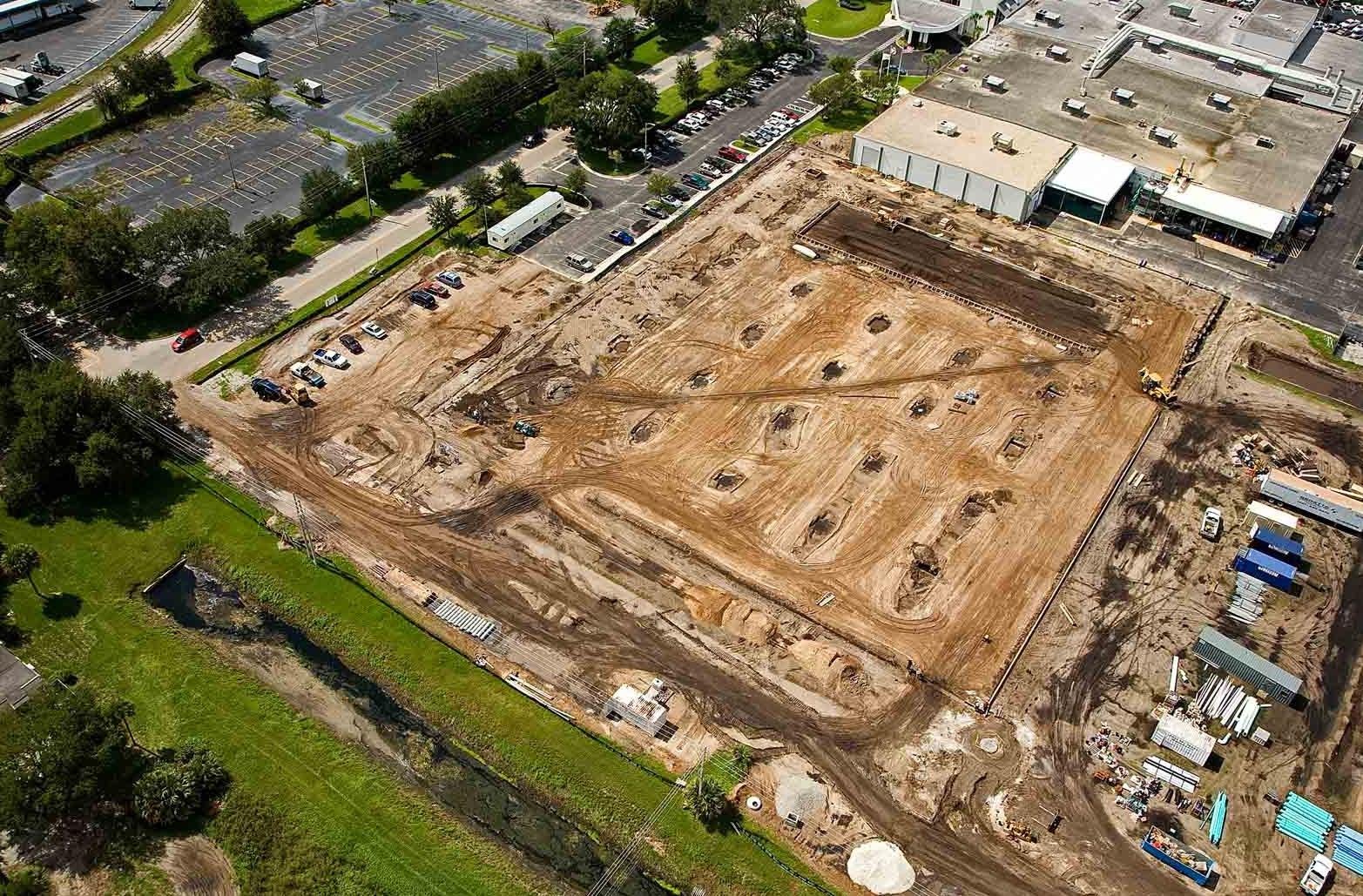
[Above: Orlando Service Center's Expansion 2007]
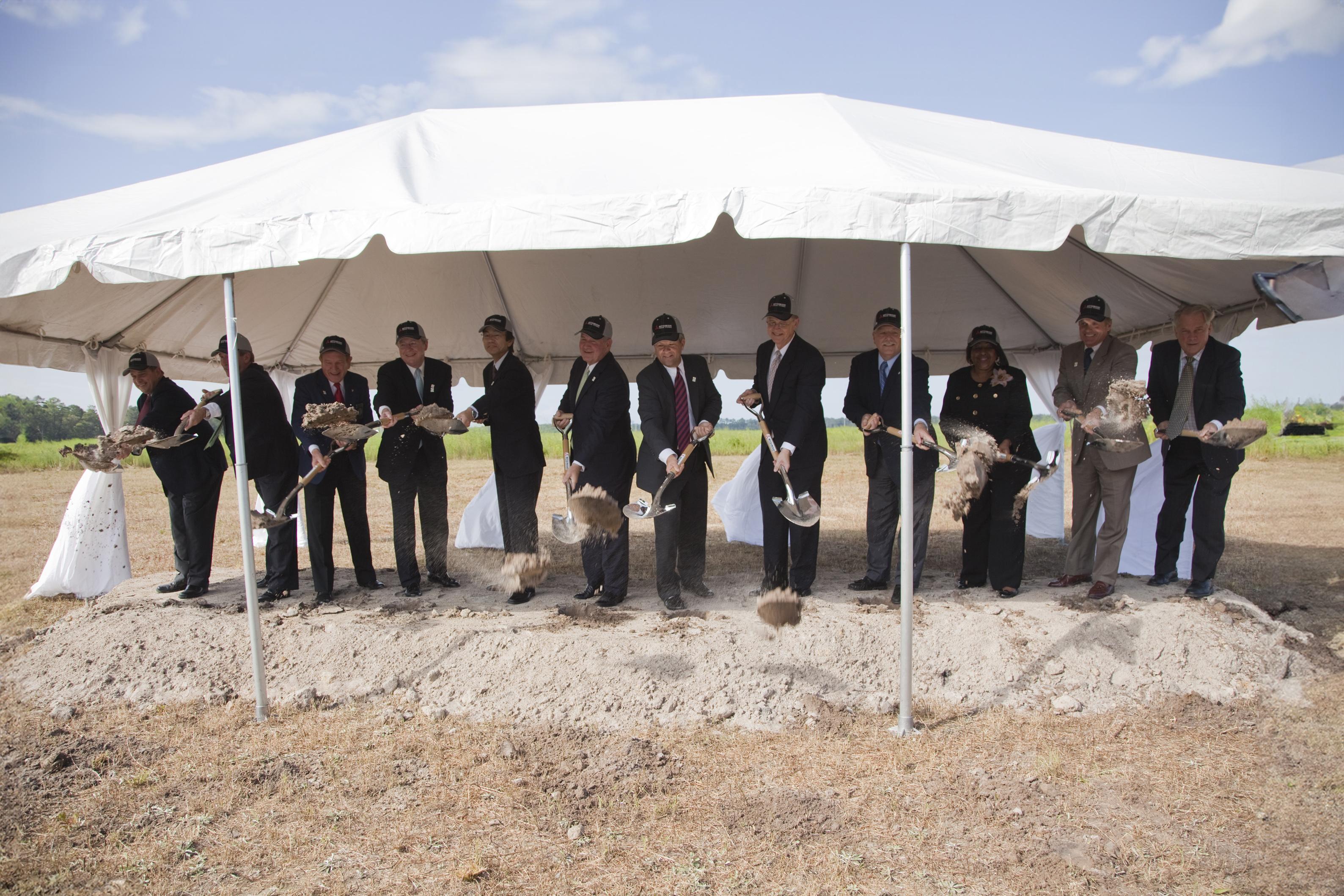
[Above: Savannah Machinery Works Groundbreaking 2009]
Our Impact: Workforce, Innovation, and Community Investment
Today, these facilities employ over 1,000 people; engineers, skilled technicians, welders, assemblers, and other manufacturing personnel help keep the lights on for people and the world. Our team is our greatest asset, and they are committed to continuous improvement, innovation, and excellence, ensuring that we remain at the forefront of the power generation industry.
Beyond technology, innovation, and our people, our focus extends to the communities we serve. We are committed to empowering local economies, creating jobs, and supporting initiatives that enhance the well-being of the people we touch.
“People are the most important part of our business. Without the right people and a good, dedicated team, there would be no parts or turbines to build,” Venckauskas says seriously. “These teams go above and beyond the normal call of duty to make a significant impact in areas like productivity, safety, and quality. We hold true to our values, and the only way you can do that is with the right people, the right team. Together, we strive for excellence and a brighter future—one team, one future.
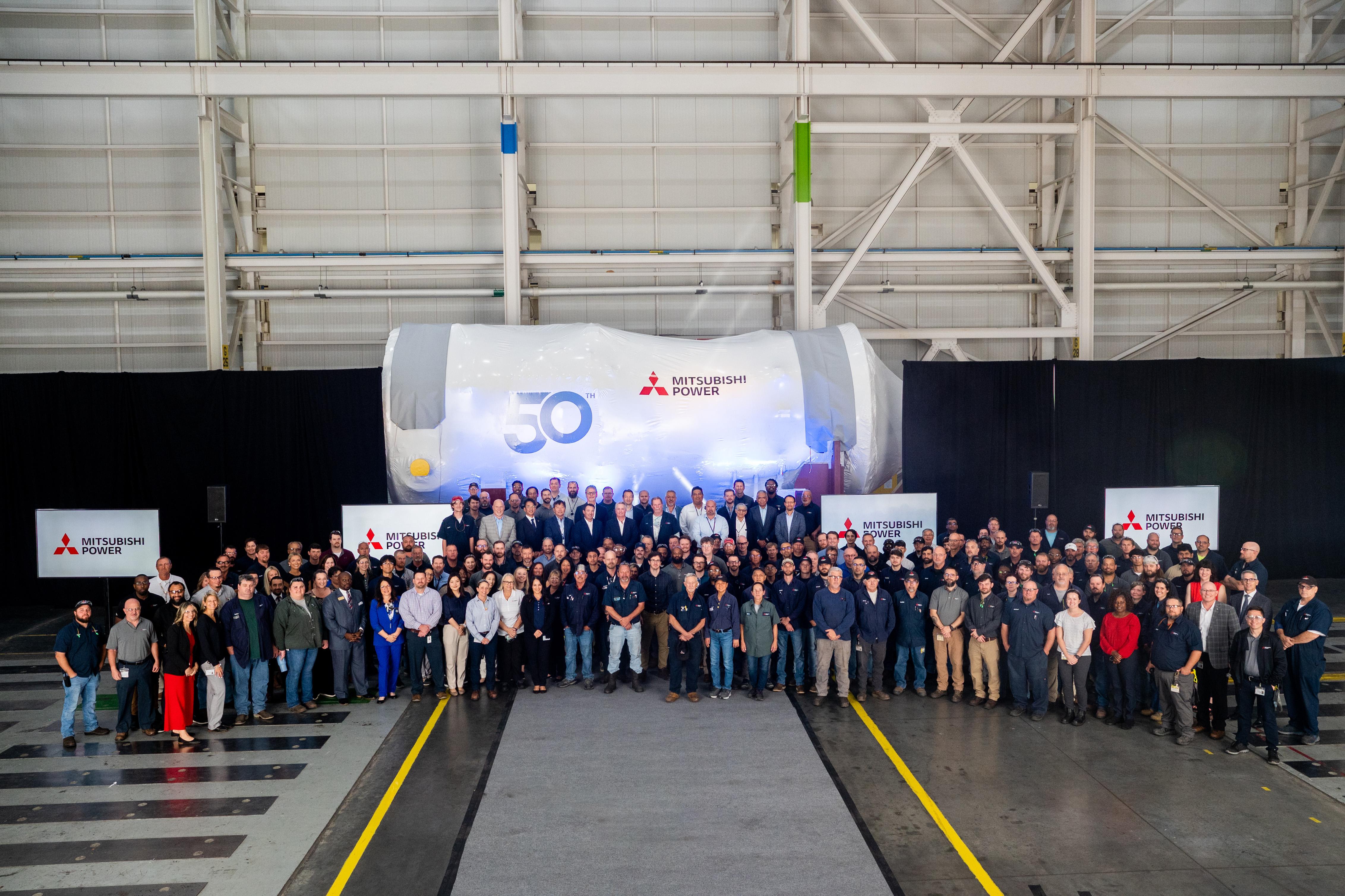