Boilers
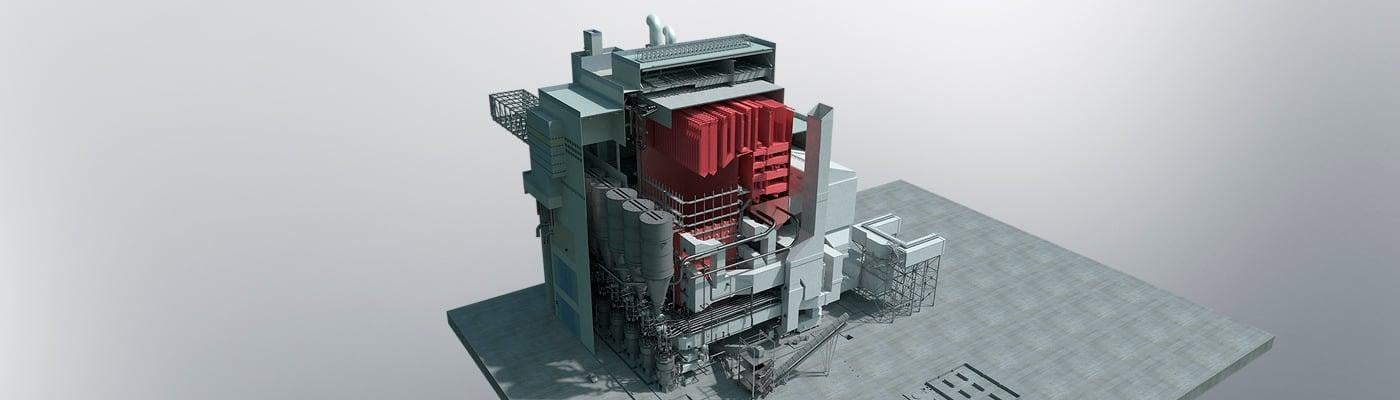
Boilers are key components of thermal power plants. They convert the chemical energy contained in fossil fuels such as coal, oil and gas into thermal energy through combustion reactions and use the resultant high-temperature and high-pressure steam-based thermal energy for supplying steam turbines used in power generation.
Mitsubishi Power supplies only boilers of the highest quality and performance, built on a vast breadth of experience and state-of-the-art technologies.
Types of Boiler
While there are various types of boilers depending on the amount, pressure and temperature of the steam they produce and the fuel they use, they generally come under one of two categories: drum boilers and once-through boilers. In a drum boiler, to ensure reliability of the furnace area, there is a drum that continually supplies water to the furnace system. A once-through boiler is a simpler structure that does not require the drum function.
In addition to once-through boilers, drum boilers and heat recovery boilers primarily used in thermal power plants, Mitsubishi Power also handles a wide range of products used in industrial applications, including bubbling fluidized bed boilers (BFB) and chemical recovery boilers used by paper manufacturers.
Overview
Once-through boilers are able to produce steam at higher pressures and temperatures than drum boilers. In steam power plants, raising steam conditions (pressure and temperature) can enable efficiency gains in power generation equipment, allowing an operator to reduce its fuel consumption and CO2 emissions
Specifications
2-Pass Boiler | Tower Boiler | |
---|---|---|
Output | Up to 1,070MW | Up to 1,100 MW |
Main steam flow rate | Up to 3,210ton/h | Up to 2,939ton/hr |
Steam temperature | Up to 600/610°C | Up to 600/620°C |
Steam pressure | Up to 31 MPa | Up to 30.5 MPa |
Benefits
Performance advantages | |
---|---|
2-Pass Boiler | Tower Boiler |
Low fuel consumption |
Proven technology and high reliability for combustion |
Lower emissions (CO2, Sox, NOx, dust, ash) | |
Less auxiliary power consumption | |
High reliability |
Technical advantages | |
---|---|
2-Pass Boiler | Tower Boiler |
Optimized for specific types of fuel | Optimized to accommodate specific types of fuel |
Various burner system layouts for good combustion | Small footprint |
Low NOx and less unburned carbon | Low NOx and less unburned carbon |
Advance combustion technology | Advanced design based on experience with coal-fired power generation in Europe |
Vertical mill for high classification performance at low power consumption | Pulverization system for lignite and low-heating-value coal combustion |
Highly durable and easy to maintain |
Overview
In a drum boiler, the circulation of water is produced through the density difference of water in the down comer pipe and the water/steam mixture in the furnace tubes. In low-pressure boilers where this density difference is large, the circulating force is high and a high volume of circulation can be ensured, but since it becomes difficult to maintain sufficient circulation volume when the density difference between the two drops due to higher pressure, a pump (BCP) is installed in the down comer pipe to supplement circulating force. The type that circulates water using only the density difference is called a natural circulation boiler, while the type that includes a pump is called a forced circulation boiler.
Overview
A heat recovery steam generator (HRSG) is one of the major pieces of equipment in a gas turbine combined cycle power plant that boasts a high thermal efficiency and produces minimal CO2 emissions. An HRSG is a kind of heat exchanger that recovers heat from the exhaust gases of a gas turbine to an extreme degree. The heat is recovered in the form of steam which is served as the power source of a power-generating steam turbine.
Benefits
- High Performance and High Reliability
- Highly economical
Overview
A bubbling fluidized bed (BFB) boiler is a boiler that can also handle fuels that are difficult to pulverize or less combustible. The fuel is introduced into a mixture of sand flowing at high temperatures, allowing the fuel to be efficiently combusted.
Benefits
- High fuel flexibility
- Reliable bed drain discharge system
- Low NOx combustion
Overview
A chemical recovery boiler is a type of biomass boiler that combusts black liquor produced as a by-product in the pulp manufacturing process at paper mills. Black liquor is a fuel derived from wood chips and is regarded as renewable. A chemical recovery boiler not only effectively uses the thermal energy gained by combusting black liquor, but also recovers sodium (carbonate) ingredients that are reused in the pulp manufacturing process, and thus plays an important role in a pulp manufacturing plant.
Benefits
- High-pressure, High-temperature Steam Conditions
- Corrosion Protection
- Low NOx combustion
Boiler Services
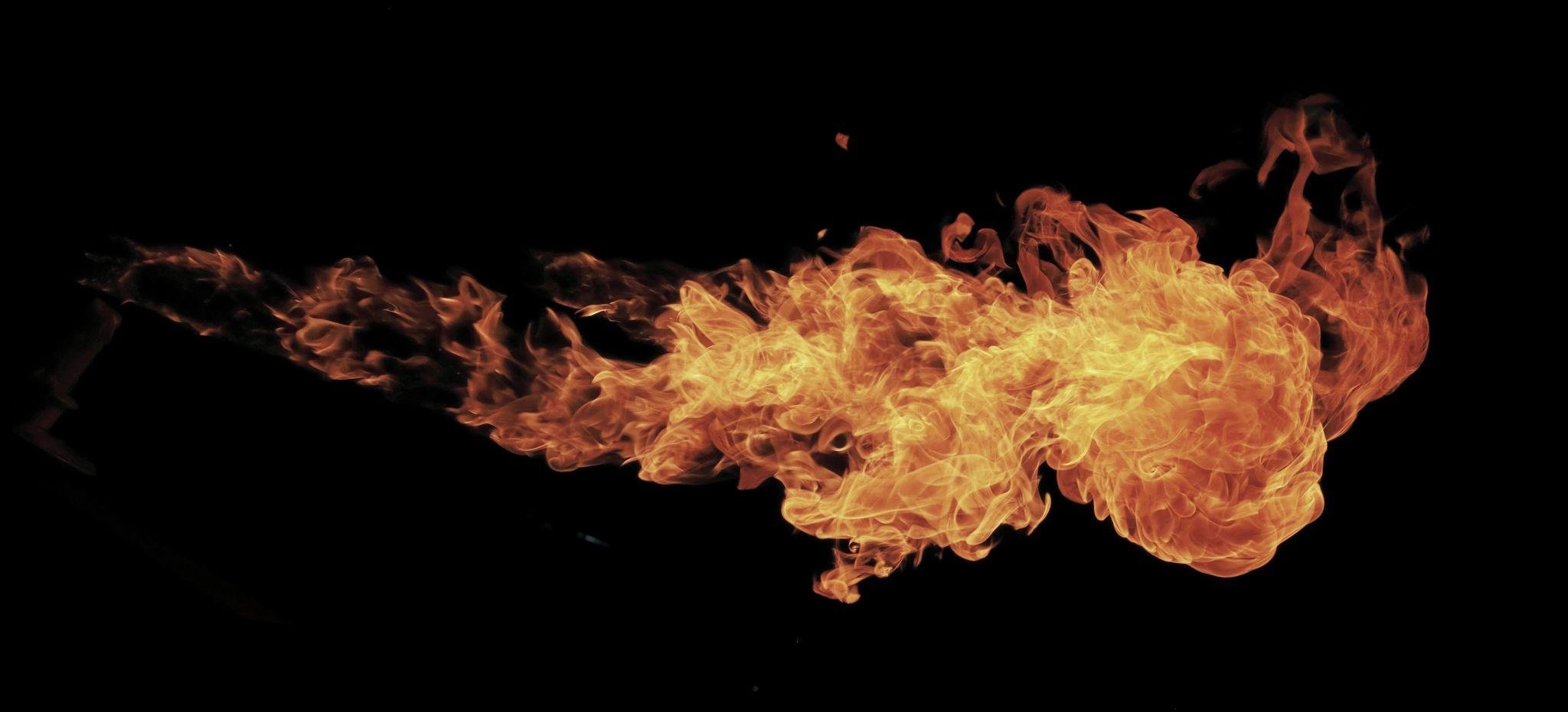
Low NOx burners
Mitsubishi Power maintains proprietary boiler technologies designed to achieve high reliability and reduce environmental impact. We offer low NOx burner technologies for solid, pulverized fuels by combustion method and different firing systems.
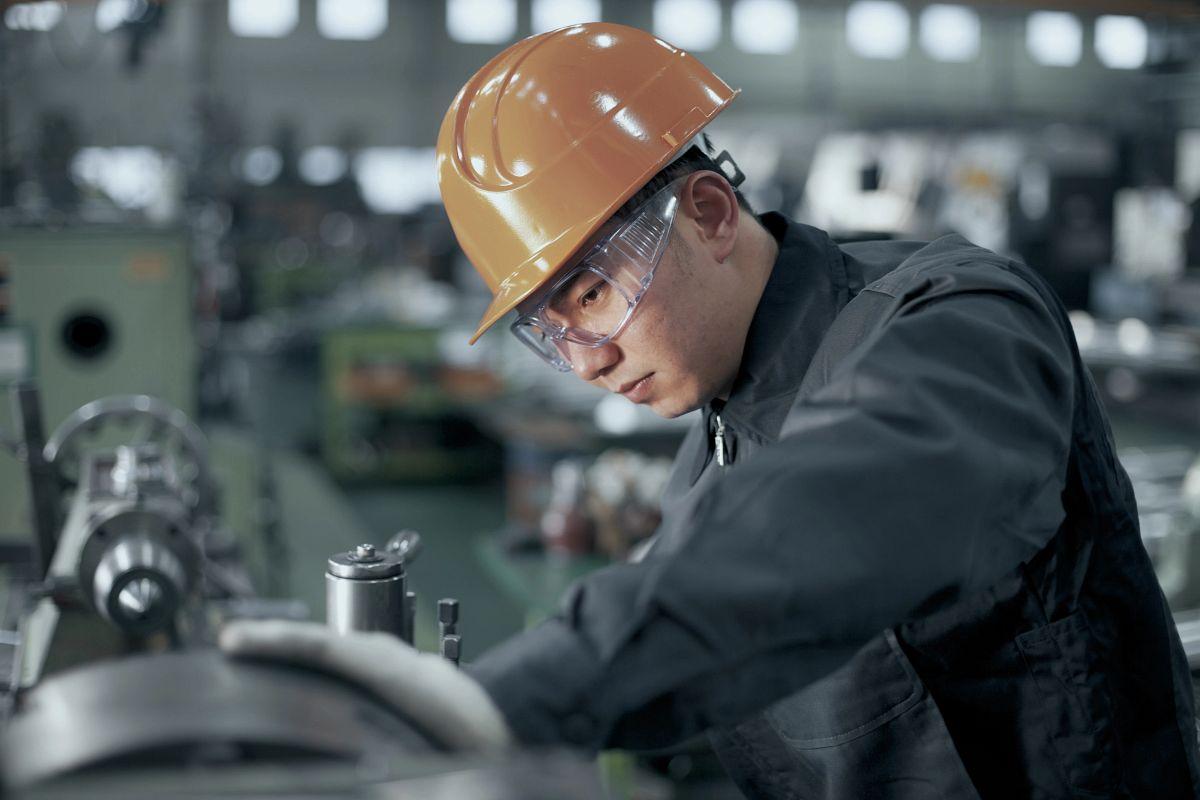
Coal to Gas Conversion
Mitsubishi Power offers boiler conversion programs to achieve CO₂ emission reduction targets. A boiler conversion involves a modification of the burner technology and a change of coal or oil to gas. While switching to gas as a fuel does not increase the efficiency of the steam plant, it does reduce CO₂ emissions.
Benefits
- Reduction in CO2 emissions in excess of 40%
- Least expensive way to transition from coal to a more environmentally friendly fossil fuel
- Bulk of the work associated with conversion/additions can be performed with the unit in operation
- Final tie-in outage in the range of 30 days
- Minimum impact to operating staff (Simplified, more reliable unit operation)
Related Articles
Step into the Future of Power Generation
Want to learn more about Mitsubishi Power Americas? Contact us today.
Contact Us