ARTICLE
Mitsubishi Power’s North American Manufacturing:Case Studies in Continuous Improvement
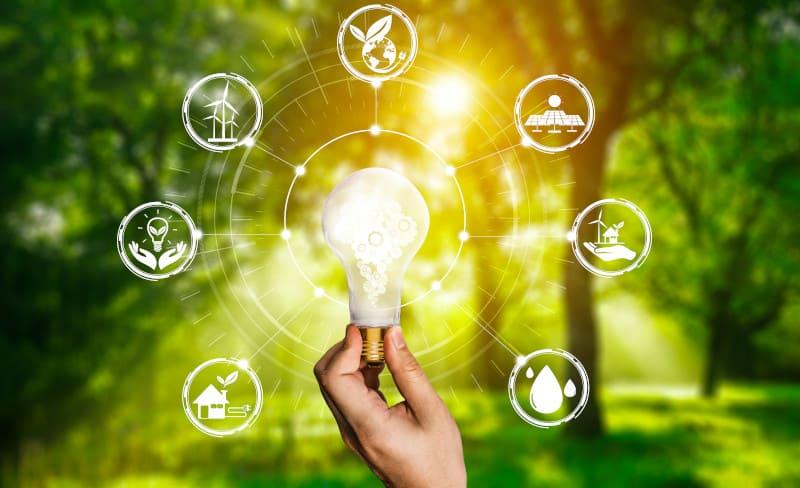
Building pathways to a decarbonized future is not a linear process. We all know now, perhaps better than ever, that things can sometimes change overnight. What is best practice and a good idea today might not hold up to scrutiny the next day. Those of us in the industry know that it takes a little bit of gumption to constantly ask the questions: What are you doing, What are we doing, and What can we do together; and that it takes outright bravery to pursue and follow up to the answers of those questions. But doing so is the spirit of kaizen, the process of continuous improvement, and the ethos of Mitsubishi Power.
One “place” that doesn’t shy away from this ethos is Mitsubishi Power’s North American manufacturing facilities. Although comprised of two sites: Orlando Service Center (OSC) and Savannah Machinery Works (SMW), the sister locations work in tandem for future-focused environmental solutions. Together, OSC and SMW aim to put best practices forward – from identifying ways for continuous improvement, to creating best practices for a particular issue, to evaluating the efficacy of those solutions once they’re implemented – realizing that doing so is a cycle, not a destination.
That journey is sometimes accomplished much like mountain climbers working together to summit. Give and take, tethered together but working and reaching separately. That journey has manifested itself in a number of ways over the years. For example, some shared initiatives between these two sites include: switching to LED lightbulbs, using solar power, and providing vehicle charging stations to employees. OSC and SMW are in different stages of all these practices, with OSC already providing LED changes and vehicle charging to the site, and solar panel implementation in progress. SMW has the first wave of LED changes complete and is in the research phase of both solar panel implementation and vehicle charging. Although nearly 300 miles separates the two sites, they are constantly in communication with one another, asking those central questions: What are you doing, What are we doing, and What can we do together?


So all that answers the last question. But today, our primary focus is on the first two of those questions. Today, we will provide a case study from both OSC and SMW to demonstrate just how innovative both places continue to be, and how both reject complacency in the face of environmental solutions.
Let’s go back to Savannah, Georgia for a bit. SMW, as we recently covered, implemented bioremediation tactics to clean stormwater of oils and greases. Savannah is a mixture of future-focused environmental solutions placed in the middle of swampland Eden. Places like SMW deal with the issues of tomorrow while facing just what’s at stake directly outside. The southern pragmatism that proved so efficient in the bioremediation strategy is now being applied to other things as well. This story starts with packing peanuts. Packing peanuts have always been problematic for SMW. In the past, when the peanuts were disposed of in the open-top general waste dumpster, they would often become airborne and be spread into the environment, creating a negative environmental event. SMW would get droves of these packing peanuts, and since the polyfoam (polystyrene) would come from vendors, there was no real way for SMW to anticipate the regulation of how much would come in, or when, and at the end of the day polyfoam isn’t really recyclable. But it was out of control, and something needed to be done. The proposed solution was to package the peanuts and use a mobile compactor to dispose of the waste. The idea was that the compactor could compress the packing peanuts to reduce volume and make disposal more efficient. On paper it seemed like a good process – collect trash, compact it, load onto a truck and go to the landfill fewer times. But pretty quickly, we ran into a problem.
The day came, and hopes were high. Everything was poised and ready, and the compactor went off. Then, something strange started happening – it started snowing, and it doesn’t snow in Savannah. They quickly realized what had happened. The smashed polyfoam had been crushed into small pieces and was quickly spreading into the environment – the exact opposite of what they had wanted. They quickly worked to clear the negative environmental impact. It was critical that they did this quickly and thoroughly to avoid impacting their stormwater drainage system and becoming a threat to surrounding grassland, forest, pond, and even bird nests. It was clear that a mobile compactor was no longer an option, but the issue still remained. What was to be done?
Joey Williams, an engineer, and Robert Lamb, EHS Specialist, got together to troubleshoot. The solution was this: “melt” the packing peanuts down using acetone and morph them into bricks. Using this method, one large tote of these peanuts (which take up volume and cause a negative environmental impact) is reduced down to a small, hand-sized brick. Then, those bricks are easily disposable. Robert was the one to come up with the central idea. He recalled that popular grade-school science experiments will show you that polyfoam (polystyrene) will dissolve in acetone, much like an effervescent tablet does in water. This got SMW thinking, and from there, it was just old-school trial and error. The next bit was just testing – determining how little acetone was needed to dissolve the packing peanuts into a malleable, but not completely dissolved, paste. It worked.
The next step was to take the gelatinous odious organic matter (commonly known as goo) and turn it into something relatively solid again so that it could be transported. Acetone evaporates in air, so all that needed to be done was to let the buckets of paste sit overnight. Then, SMW rolled the dissolved packing peanuts into little balls, reducing the original volume by about 98%. And that was that! Once the hardened packing peanut balls are dry, they can be safely transported and disposed of. Through this process, SMW takes cubic yard boxes of polyfoam and transforms them into a hardened thin layer. The process was a success, improving things from both an environmental and economical standpoint, but with the primary emphasis being that it greatly ensures our long-term environmental impact is reduced once the peanuts leave the facility.
About 300 miles south of SMW, the spirit of kaizen was alive and well at the Orlando Service Center. Here, the OSC was looking for solutions to improve their wastewater treatment process. Waste practices were solid: all the trash from OSC (lunchroom trash, office trash, etc.) would be collected, taken to a compactor, and sent to a company, who would burn the waste and convert it into electricity. None of it would go to a landfill, and it was all compacted garbage that was turned into power.

OSC’s wastewater, on the other hand, was a more difficult process to perfect. In general, wastewater is an interesting and difficult waste medium to tackle, because applicable strategies for improvements are highly reliant on the particular needs of a facility, which are determined by the particular waste stream in that area that uses those facilities. Therefore, there’s not a set method or equation to implement across all facilities needing improvements, and there’s a level of creativity involved in each of these implementations.
The standard process at OSC was to collect non-recyclable or non-reusable wastewater and move approximately 20,000 gallons a week on a truck to be transported to a proper waste handling facility. The OSC generated hazardous wastewater that had to be neutralized to a nonhazardous state. They then had the wastewater shipped offsite to their waste contractor facility. They lacked the appropriate approval from the county to discharge through the sanitary sewer system due to required monitoring, mapping and discharge/sample ports. The transportation was all done via tanker truck, which would move wastewater three times a week at $300 a transport and $0.31 per gallon. OSC knew there was a better answer out there.
Two years ago, the seed was planted. The idea was to update the system, making it more automated to remove human error and handling of the chemicals involved. Most of the wastewater at SMW was rain run-off contaminated with oils and greases, and using bioremediation was a clever solution to clean up that particular issue. But at OSC, the situation and its requirements were a little bit different, and bioremediation was not a feasible tactic to render the wastewater to a nonhazardous state suitable for discharge. The new system was officially implemented this spring, and so far, in every metric: cost, safety, and efficiency, the new system is a vast improvement. For one thing, the new, updated system was properly mapped, and the required monitoring and sample ports were added, per the proposed discharge permit requirements. The cessation of using the truck means that, aside from the economic cost savings there is a significant emissions reduction. In short, this is the most environmentally responsible path Mitsubishi Power could take as a solution to this problem.
Both these case studies serve as a reminder that our concerns for the earth and the environment extend beyond days set aside to celebrate such things. For us, every day is Earth Day. Every month is Earth Month. We are always looking for environmentally-friendly solutions, every day, at every level – but there are also solutions, every day, at every level. That is the spirit and strength of kaizen at Mitsubishi Power.