ARTICLE
How Mitsubishi Power and J-POWER USA worked together to bring the first M501JAC™ units to North America
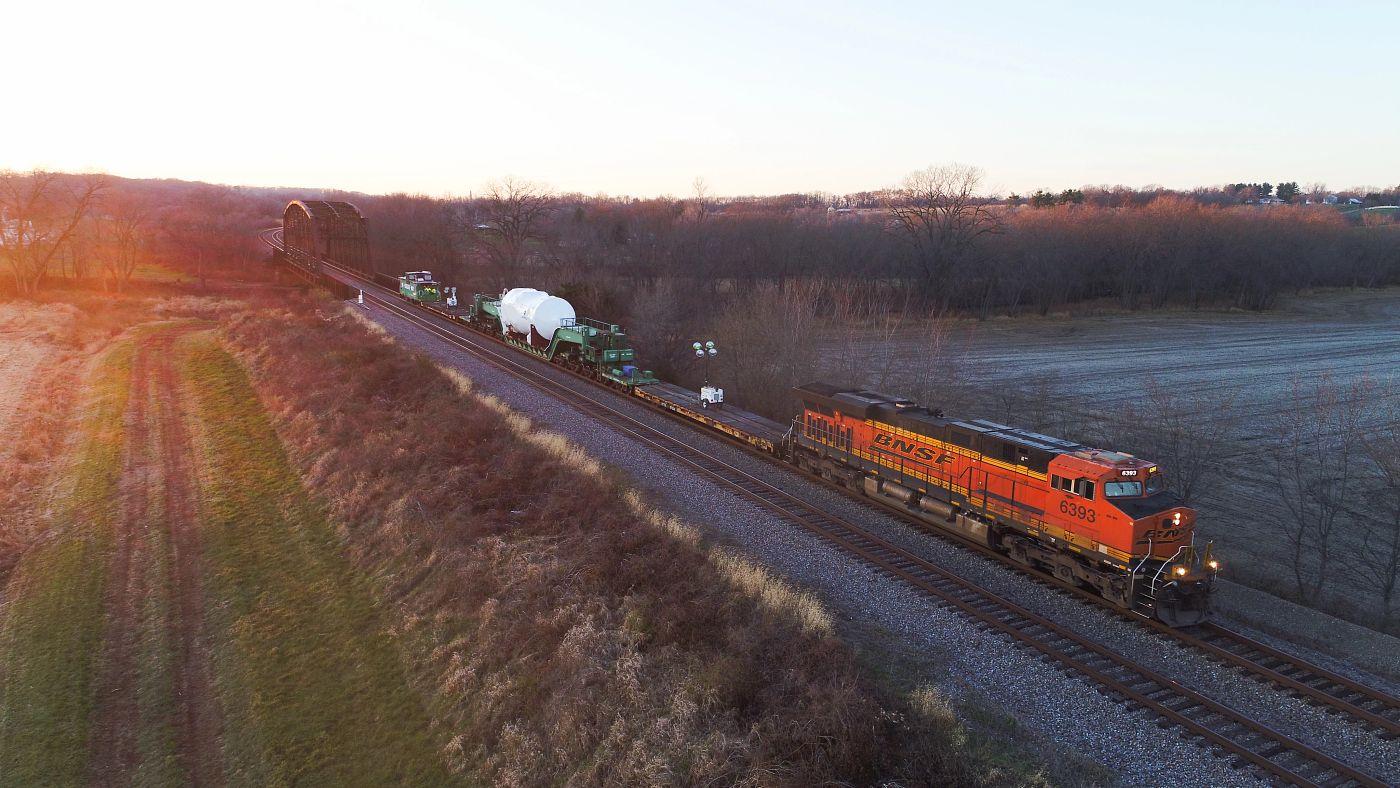
The Energy Transition Takes More than Technology. It Takes Human Connections.
Kevin Miller’s office is lined with pictures of the power plants he’s helped commission over the years. The photos remind Miller, Vice President of Asset management, operations, and construction at J-POWER USA, of the communities where he’s had a hand in making it possible for people to turn on their lights, heat their homes and go about their daily lives.
He learned the vital role that reliable power plays as a boy, watching his father go off to build coal plants. Like the one in Delta, Utah, that’s proudly featured in another photo in the office gallery.
Kevin’s career has focused on gas-powered electrical generation, which has largely supplanted the coal plants that predominated during his father’s career. Today, as the grid continues to change rapidly, power producers and distributors are adapting to accommodate a range of intermittent renewable power sources. And that need to keep evolving prompted J-POWER USA in 2015 to begin planning a new combined-cycle power plant in Elwood, Illinois, 50 miles outside Chicago.
They called in Kevin to run the project.
The J-POWER USA team crosses the globe
Kevin had spent nearly 30 years in engineering, construction, and project management and had a hand in commissioning numerous plants. He was familiar with the process involved with building a facility and the caliber of equipment needed. He and the J-POWER USA team knew that selecting the right turbine technology – and the right partner to provide it – would be critical. After several years planning, vetting, and analyzing their options, the team selected Mitsubishi Power as their partner of choice for the first two M501 JAC gas turbines made in North America – serial numbers 1 and 2. They were that confident in the company and its technology, as well as its ability to ensure the efficiency, longevity, reliability, and adaptability needed for future demands.
A trip to Mitsubishi Power’s 250-acre Takasago Machinery Works demonstration facility in Japan proved essential. It was here that Miller and the J-POWER USA team first scrutinized a JAC unit in operation. They knew the JAC units – Mitsubishi Power’s largest and most efficient gas turbines – had cutting-edge capabilities, able to start quickly – reaching maximum capacity in as little as 30 minutes in a combined-cycle system. The flexible turbines can adjust their output to handle fluctuating electricity demand and can run on a mixture of 30% hydrogen without major modifications. That critical combination of flexibility and reliability made a compelling case for the units’ longevity in a fast-changing industry.
The Takasago visit bolstered the J-POWER USA team’s faith in the JAC units and Mitsubishi Power. They witnessed firsthand the company’s embrace of Kaizen, the Japanese philosophy of continuous improvement. By the time J-POWER USA made its decision, the JAC unit had logged 8,000 hours of operation, during which Mitsubishi Power’s engineers monitored, refined, and improved the model. The intense attention to detail and commitment to quality assured the J-POWER USA team that these turbines, and an ongoing relationship with Mitsubishi Power, would best position them to navigate the energy transition.
“It was a real eye-opener for me – the fact that Mitsubishi Power has the engineering, the manufacturing, the operational plant and the research team dedicated to improving the way this equipment operates blew me away.”
– Kevin Miller, Vice President, Asset Management, Operations, and Construction, J-POWER USA
Collaboration counts
From the beginning, J-POWER USA and Mitsubishi Power laid the foundation for a successful project in Elwood. Creating a shared vision and set of values is a hallmark of Mitsubishi Power’s long-term work with customers, says Tommy Carl, Sales Director at Mitsubishi Power. Early on, the team agreed to a collective set of long-term objectives and committed to honest conversations throughout what they knew would be an intricate and extensive effort of over more than two years.
The company’s focus on constructability in its manufacturing processes exemplifies this kind of collaboration. Manufacturing large, intricate blocks of the system in the controlled environment of a plant is like building a prefabricated house (but infinitely more complex). Shipping modules as large as 30 feet high by 50 feet long to the site reduces risk, cost, and time by improving overall safety and limiting the amount of wiring, welding, and other construction that could be disrupted by bad weather. In the past, all the fuel, gas-related piping, valves, and wiring had to be built on site piece by piece. Now, it’s just a matter of interconnecting the modules with piping and connecting cables. Assembly that used to require more than 80 high-pressure welds that could take up to five days each to complete only requires around a dozen such welds.
That flexibility became particularly important when the pandemic disrupted global supply chains just as the construction of the plant got underway. One day, recalls Miller, he sat in his office incredulous at the mounting challenges. The plant was like no other he’d worked on. “I had my head on my desk wondering how we were going to get through this,” he says.
Week by week, the team persevered and came up with one creative solution after another. Mitsubishi Power collaborated with J-POWER USA to keep team members safe while getting modules in place to keep construction on track. They carefully sequenced the delivery of parts to the construction site and dispatched technical field assistants to Elwood who kept assembly moving smoothly despite tight schedules and reduced manpower due to COVID protocols.
Ultimately, Jackson Generation Power Plant commissioned on schedule in spring 2022 — a monumental achievement given the circumstances amid a global pandemic.
Building a plant, and a long-term relationship
It’s been two years since the plant began powering homes in the Elwood community, and the collaboration between the companies continues today. Mitsubishi Power remains highly engaged in the Jackson operation, from 24/7 monitoring of the site through TOMONI HUB, Mitsubishi Power’s remote monitoring center, to helping the J-POWER USA team diagnose issues and maintain the equipment.
“If we have an issue, we reach out to TOMONI. They're open 24 hours a day.”
– Scott Freese, Plant Manager, Jackson Generation
Achieving results like this takes personal connections between equipment manufacturers, equipment operators and the communities they both serve. In a rapidly changing world, such relationships go a long way toward solving urgent and intricate problems and ultimately improving lives. “Kevin can call me whenever he needs anything,” says Mitsubishi Power’s Carl. “I look at him as more than a customer – he’s a friend.”
For Miller, these personal connections run even deeper. In his office, near a picture of J-POWER USA's completed Elwood plant, he also keeps the picture of a coal plant his father helped construct, the Intermountain Power Project (IPP) in Delta, Utah. Recently, engineers from that plant came to Elwood to see the JAC units in action – a step in their own diligence as they plan to decommission that plant to construct a natural gas plant with two JACs that will eventually run on 100% green hydrogen.
It was a proud moment for J-POWER USA, sharing their success with peers. And it was a poignant moment for Kevin, tying together two plants that two generations of the family helped build and epitomizing progress in the energy transition. But the connections to power don’t end there: Kevin’s son recently entered the industry. He’s working on a solar installation in Las Vegas — continuing the family’s legacy of helping people and communities keep the lights on.
###