Flue Gas Desulfurization (FGD) Plants
-
Max. Capacity
1,050 MW
-
Max. Inlet SO2 Concentration
80,000 mg/Nm3 (Coal fired)
-
Max. SO2 Removal Efficiency
99%
-
High Reliability
The flue gas desulfurization (FGD) plant removes sulfur dioxides (SO2) from flue gas produced by boilers, furnaces, and other sources. Mitsubishi Power effectively contributes to the prevention of air pollution through its wet limestone-gypsum FGD process and seawater FGD process, and both processes can treat a large range of SO2 concentrations for greater plant reliability and economics.
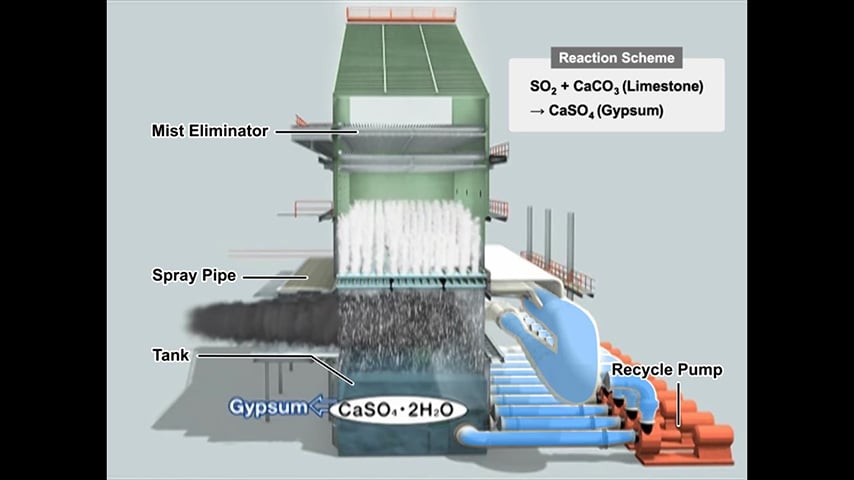
Features
We have supplied more than 300 FGD plants worldwide and have acquired a larger market share by offering the following features:
- High SO2 removed efficiency meeting required emission standards for all kinds of fossil fuels
- Multiple pollutant control with associated environmental control equipment
- High reliability
- Energy and utility savings
Wet Limestone-Gypsum FGD Process
This process is suitable for large-scale flue gas treatment, and can uses a low cost absorbent (limestone), and produces stable and valuable by-products (gypsum).
Typical system flow is shown below.
Scrubber Types
Mitsubishi Power offers two types of scrubbers: one is a double contact flow scrubber and the other is a spray tower scrubber. The optimal scrubber type is selected based on flue gas conditions, site layout, etc.
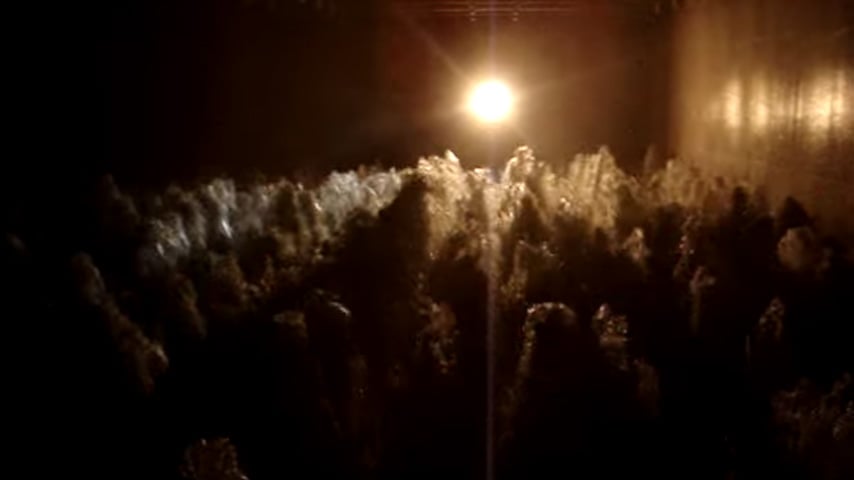
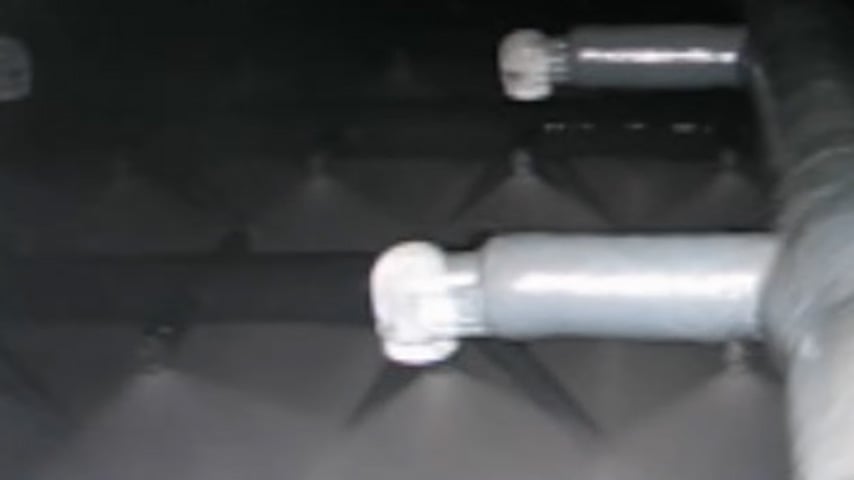
Application
We have delivered over 300 FGD plants under the following conditions.
Desulfurization Efficiency | 70 thru 99% |
---|---|
Dedusting Efficiency | 70 thru 90% |
Coal, Lignite | 750 thru 22,000 mg/Nm3 (260 thru 7,700 ppm) |
---|---|
Oil, VR, etc. | 700 thru 16,000 mg/Nm3 (240 thru 5,600 ppm) |
Sintering | 700 thru 84,000 mg/Nm3 (240 thru 29,400 ppm) |
Seawater FGD Process
This process can be applied in regions with soft regulations on SO2 emissions and initial cost is lower than the wet limestone-gypsum FGD process due to the simple equipment configuration.
Typical system flow is shown below.
Major Components of Seawater FGD
The seawater FGD consists of two major components : grid tower scrubber and the aeration basin. In the grid tower scrubber, seawater absorbs SO2 from the flue gas. In the aeration basin, the SO2 rich seawater is treated to make it suitable for discharge to back to the sea.
Application
We have delivered seawater FGD plants under the following wide conditions.
Desulfurization Efficiency | 70 thru 98% |
---|---|
Typical Inlet SO2 concentration | 650 thru 5,300 mg/Nm3(230 thru 1,900 ppm) |
Typical Capacity | 370,000 thru 630,000 Nm3/h |
Fuel | Coal, Oil, etc. |
Products
- GTCC
- Steam Power
- IGCC
- Geothermal
-
Gas Turbines
- Product Lineup
- Comparative Performance
-
Technical Information
- Gas Turbines for Mechanical Drive Applications
- Cutting-Edge Elemental Technology Producing 1600°C Class J Gas Turbines
- Development of High-Efficiency Gas Turbine Applying 1600°C Class J Technology
- Combustor Technologies Supporting Stable Operation
- Overview and Verification Status of T-Point 2 Demonstration Facility
- Comprehensive Efforts from Development to Manufacturing
- Summary of Orders
- Development History
- Product Selection Assistant (Middle & small Class)
- Aero-derivative Gas Turbines
- Steam Turbines
- Boilers
- Air Quality Control Systems (AQCS)
- Generators
-
Control Systems
- What is DIASYS?
- DIASYS Netmation
-
DIASYS Optional Products
- IR-S Infrared Flame Detector
- Net IR-S Infrared Flame Detector
- Rail Mounting Net IR-S
- Boiler Tube Leak Detector
- Shaft Vibration Analyzer
- Simulator
- Advanced Combustion Pressure Fluctuation Monitoring System (A-CPFM) / Combustion Pressure Fluctuation Monitoring System (CPFM)
- Multi-Coal Fired Boiler Optimum Control
- FXtoLS Adapter
- Fuel Cells
- Additive Manufacturing
- Catalogue
- HIACS Series
- Technical Report