Integrated Coal Gasification Combined Cycle (IGCC) Power Plants
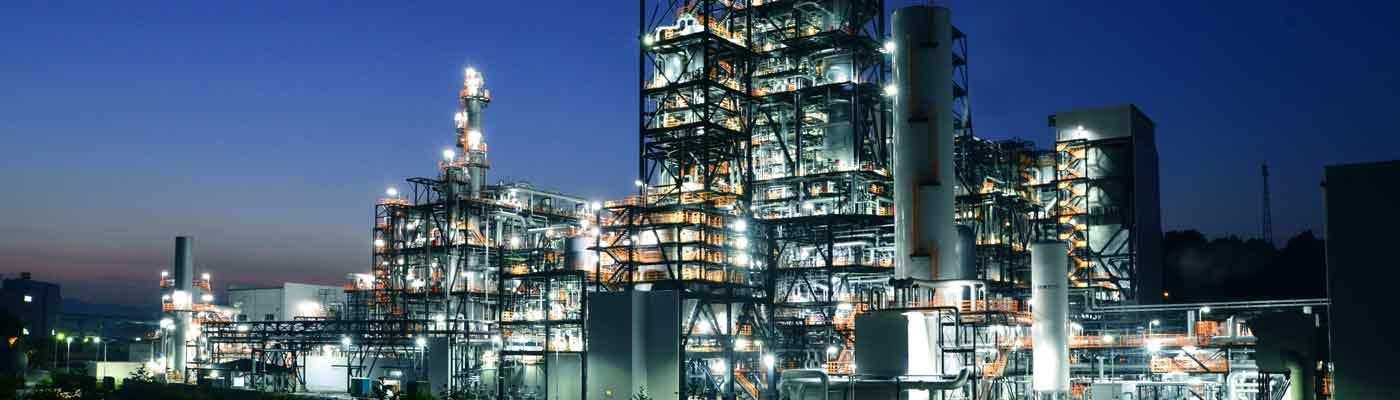
-
World-class Power Generation Efficiency
48% LHV
-
Low Grade Coal is Applicable.
Coal Flexibility
-
Low NOx, Low SOx and Low Dust Concentration
Superior Environmental Performance
-
CO2 Emissions Compared with Those of Conventional Coal-fired Thermal Power Generation
About 15% Lower
Next-generation power generation system characterized with coal gasification for high efficiency and environmental performance
A Power Generation System with High Efficiency
Integrated coal gasification combined cycle (IGCC) power plants are a next-generation thermal power system with significantly enhanced power generation efficiency and environmental performance due to its combination with coal gasification and the Gas Turbine Combined Cycle (GTCC) system. Large-type IGCC systems can improve power generation efficiency by approximately 15% and reduce CO2 compared with conventional coal-fired thermal power systems.
IGCC=Integrated coal Gasification Combined Cycle
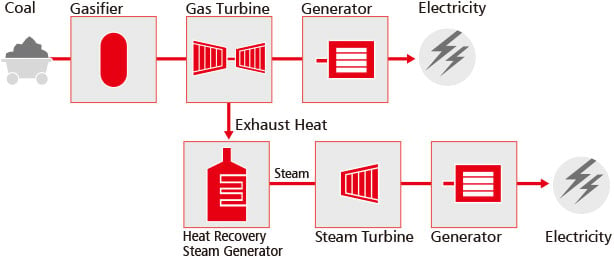
High Environmental Performance
With enhanced system efficiency, IGCC lowers SOx, NOx and dust emissions per kilowatt-hour of electric power generated. It discharges hot wastewater that is about 30% smaller than the conventional coal-fired thermal power generation.
While the flue gas desulfurization equipment in conventional coal-fired thermal power generation required a large amount of water for treating flue gas after fuel operation, IGCC consumes a much smaller amount of water because it treats fuel gas that is higher in pressure and smaller in volume.
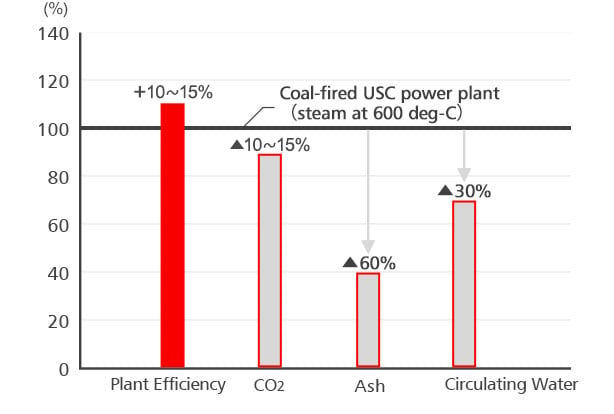
Our IGCC Business
Mitsubishi Power retains two types of coal gasification technology, namely, air-blown and oxygen-blown technologies, and leads the world in terms of its technological capabilities. In line with expectations that the need for the IGCC system will increase further due to its ability to both effectively utilize coal resources and protect the environment, this system has been gaining attention around the world.
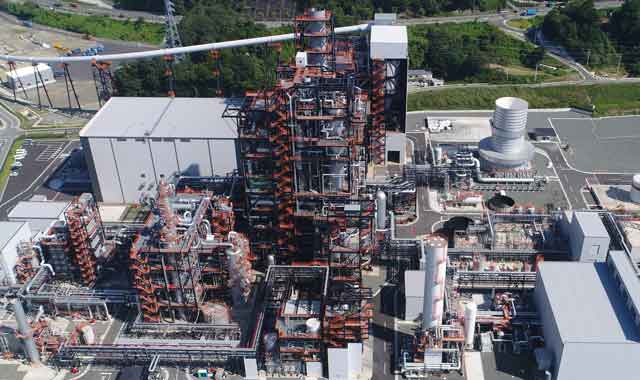
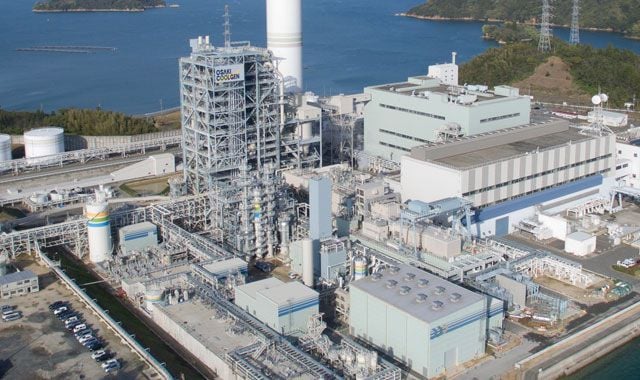
System Configuration
Air-blown IGCC systems use air for coal gasification.
First, coal is processed into coal gas in the gasifier, where air is used as the gasification agent. Coal gas undergoes desulfurization and dedusting treatment in the gas clean-up unit to comply with the standards for gas turbine fuel and exhaust gas. The cleaned gas is supplied to the gas turbine combined cycle (GTCC) facility.
The gas turbine combined cycle (GTCC) facility burns the cleaned gas as fuel to turn the gas turbine for power generation. The heat of the exhaust gas is recovered at the heat recovery steam generator (HRSG) by heat exchange with water and the generated steam drives steam turbine for additional power generation.
Placed downstream from the gasifier, the heat exchanger cools the hot coal gas. At that time, steam is generated. It is merged into the HRSG and used for power generation with the steam turbine. It further increases power generation efficiency.
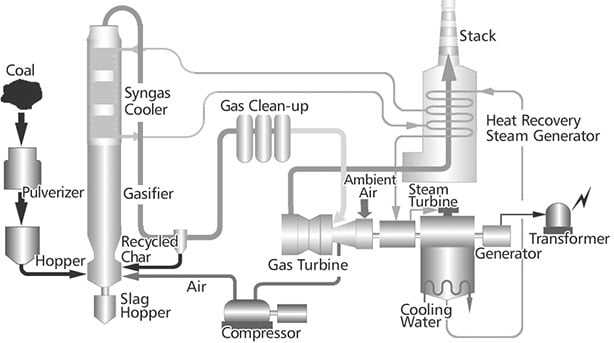
Air-blown Gasifier
The air-blown gasifier causes a reaction between the supplied coal with a gasification agent to generate high temperature combustible gas mainly composed of carbon monoxide (CO) and hydrogen (H2).
The gasifier has a two-chamber two-stage structure, consisting of a combustor at the lower (first) stage and a reductor at the upper (second) stage. Securing the calorie amount of gasified coal gas necessary for operation of the gas turbine, it melts ash and discharges it smoothly. Therefore, it plays two different roles at the same time.
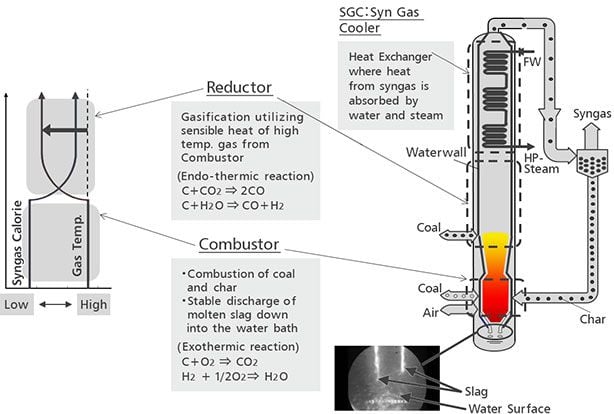
Features of the Air-blown IGCC
High Power Generation Efficiency
IGCC exhibits higher power generation efficiency in combined power generation with the Rankine cycle and the Brayton cycle than in the conventional coal-fired thermal power generation with only the Rankine cycle. Gasification using air leads to lower power consumption for oxygen production and results in higher net plant efficiency.
In addition, as in natural gas-fired GTCC, higher temperature operation in the gas turbine means higher power generation efficiency. Application of a 1,600°C-class gas turbine, which has a track record in natural gas-fired GTCC, and a 1,700°C-class gas turbine under development is expected to increase the efficiency of the IGCC.
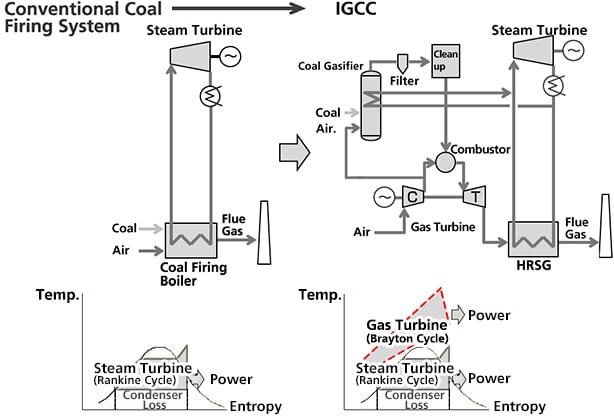
A Wide Variety of Coal Types are Applicable
In conventional coal-fired thermal power generation, it is difficult to use coal with low ash melting temperature for the prevention of slagging and fouling. In the IGCC, the gasifier melts and discharges ash. It is suited to types of coal with low ash melting temperature.
It opens the way for using types of low rank coal and petcoke that are conventionally difficult to use in power generation.
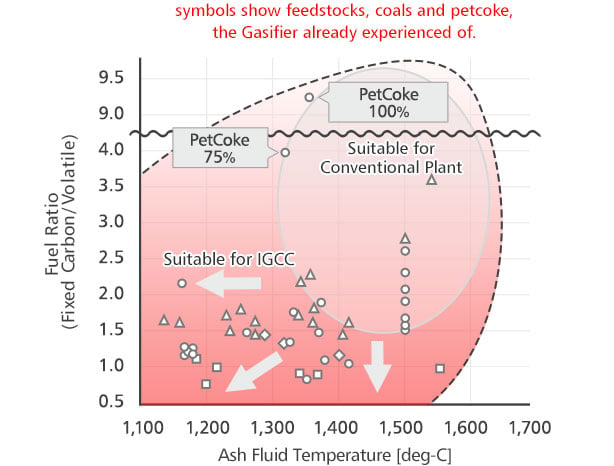
Effective Use of Slag
Conventional coal-fired thermal power generation discharges ash in the form of fly ash, whereas the IGCC releases ash in the form of glassy slag. With the same weight, slag has a volume that is half or less than that of fly ash. Given that it is glassy, slag can be effectively utilized as a material for cement and road surfaces.
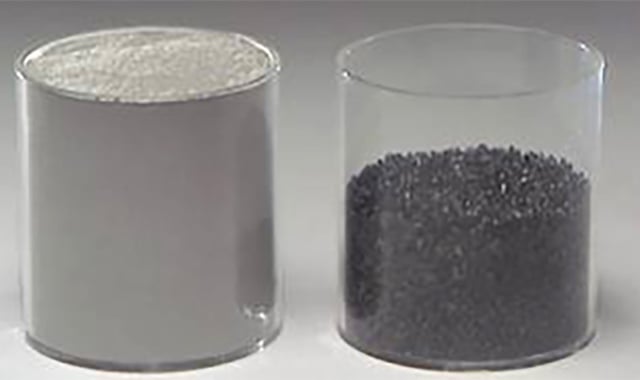
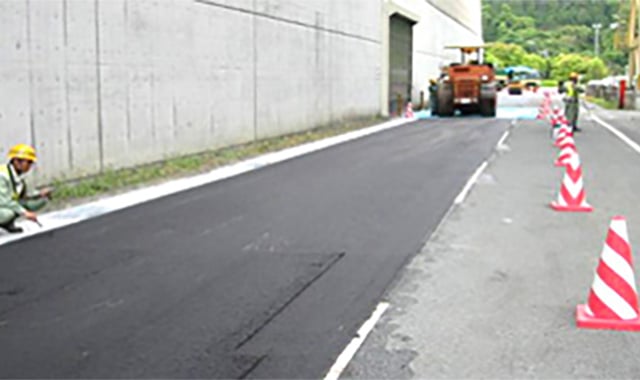
Integration
Air-blown IGCC applies following integrations for performance improvement.
- The air for gasification is bled from the air compressor of the gas turbine and pressurized with the bleed air compressor to the necessary level prior to use.
- From the water bled from HRSG, steam is generated at the heat exchanger in the gasifier and merged back into the HRSG steam line so that it may be used for power generation with the steam turbine. Heat is thus effectively utilized.
- High temperature exhaust gas from the HRSG is used for drying coal. In comparison with air drying, it results in lower oxygen concentration, a higher level of safety and suppression of a decline in efficiency to a low level.
Nakoso Power Station Unit 10 (Former IGCC Demonstration Plant)
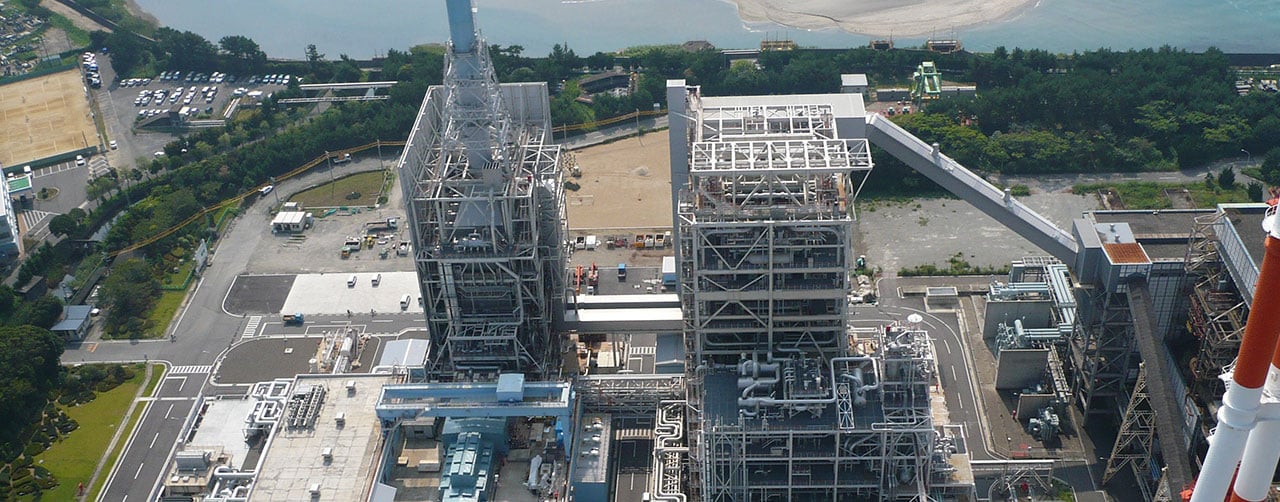
Plant facility specifications
Output | 250 MW | ||
---|---|---|---|
Coal consumption | Air dry basis | Approx. 1,700 metric tons per day | |
Method | Gasifier | Air blown and dry feed | |
Gas clean-up | Wet (MDEA) and gypsum recovery | ||
Gas Turbines | M701DA(50Hz) 1,200degC-class |
||
Target thermal efficiency | Net | 42% (LHV) | 40.5% (HHV) |
Environmental characteristics (targets) | SOx emission concentration | 8 ppm | 16% O2 basis |
NOx emission concentration | 5 ppm | ||
Dust emission concentration | 4 mg/m3N |
Implementations Towards Development and Commercialization
We have made joint development and commercialization efforts together with the national government, electric power companies and the Central Research Institute of Electric Power Industry (CRIEPI) with a view to realize air-blown IGCC technology.
A small-sized test furnace with a coal feed rate of two metric tons per day in the 1980s evolved into a pilot plant treating 200 tons per day. As a final step towards commercialization, a project with the IGCC demonstration plant with a power generating output of 250 MW was carried out. This demonstration plant project was implemented by Clean Coal Power R&D Co., Ltd., which was taken over and merged into Joban Joint Power Co., Ltd. in April 2013. The power plant was built on the premises of Nakoso Power Station of Joban Joint Power in Fukushima Prefecture. The verification test commenced in September 2007 and lasted for five and a half years.
Targets and achievements of the verification test
Target | Achievement | |
---|---|---|
System safety | Safe operation at the rated output and safe shut down in the event of emergency confirmed. | Stable operation at the rated output of 250 MW confirmed. (March 2008) |
Environmental performance | Flue gas properties (at the stack outlet) Targets of SOx: 8 ppm, NOx: 5 ppm Dust: 4 mg/m3N to be achieved |
Flue gas properties' targets confirmed met (March 2008) Results: SOx: 1.0 ppm, NOx: 3.4 ppm Dust: 0.1 mg/m3N |
Reliability | Uninterrupted operation for 2,000 hours (equivalent to three months in summer) to be attained | Uninterrupted operation of 2,039 hours attained (September 2008) After start of commercial operation, uninterrupted operation for 3,917 hours attained (December 2013) |
Coal flexibility | Stable operation using types of coal other than the designed coal (Chinese Shenhua coal) confirmed | North American powder river basin (PRB) sub-bituminous coal, Indonesian sub-bituminous coal, Colombian coal, Russian coal, Canadian coal, etc. |
High efficiency | Net efficiency target of 42% to be achieved | Net efficiency of 42.9% achieved (January 2009) |
Durability | Facility opening inspection to be conducted for verification after endurance operation for 5,000 hours |
|
Economic efficiency | Costs of construction, operation, maintenance, etc. of the commercial facility to be evaluated from a comprehensive perspective | The cost of power generation of the commercial facility may be equivalent to or lower than that of a conventional coal-fired thermal power plant. |
Operability | Enhancement of operability as a thermal power plant | Operability equivalent to the conventional coal-fired thermal power plant confirmed (March 2011) (start-up time of 15 hours, minimum load of 36%, load change rate of 3% per minute, etc.) |
After successful attainment of 2,000 consecutive hours of operation in September 2008, the verification tests such as a coal type change test, operation optimization test (including check on the thermal efficiency) and others were conducted. In June 2010, the long-term durability test (for checking reliability) reached the initial target of 5,000 cumulative hours in a year.
Set as a target in the series of operation tests, 1. Reliability of the facility, 2. Thermal efficiency, 3. Environmental performance, 4. Coal flexibility, 5. Economic efficiency of the plant In all of these items, the facility was confirmed to meet the targets. The test observed a gross output of 250 MW and net efficiency of 42.9% (LHV), confirming that both the output and the efficiency sufficiently satisfied their respective planned levels. The environmental performance was so good that it exceeded the planned level. It was verified to exhibit greater environmental performance than conventional coal-fired thermal power generation.
The coal type diversification test confirmed that the demonstration plant conducted stable single fuel operation not only with the designated Chinese coal, but also with other low grade coal such as North American and Indonesian sub-bituminous coal.
The verification test with the IGCC demonstration plant finished testing all of the items in five and a half years, and obtained all of the data necessary to design commercial models. Thus, the test was terminated at the end of March 2013. On April 1, 2013, Joban Joint Power Co., Ltd. took over the facility and put it into operation as Unit 10 at its Nakoso Power Station for two purposes. One was to use the output of 250 MW as a power supply capacity, and the other was to further refine the IGCC technology by continuing its operation. After it was put into commercial operation, Unit 10 at Nakoso Power Station achieved uninterrupted operation of 3,917 consecutive hours to mark the world' s longest continuous operating time among IGCC systems.
Commercialization
As the next step of the air-blown IGCC, we are marketing a 500,000-kilowatt class commercial unit with a large-sized gas turbine to domestic and overseas markets.
The commercial unit incorporates findings obtained from Unit 10 at Nakoso Power Station, which formerly served as an IGCC demonstration plant, to feature enhanced reliability and operability. The equipment and facility subject to verification of redundancy with Unit 10 at Nakoso Power Station were optimally designed to improve economic efficiency. We are working on researching more sophisticated operations such as greater coal flexibility and enhancement in output, efficiency and operational flexibility(*).
- ex) Load change rate :3% or more
Major specifications of the commercial IGCC unit
Item | Major specifications | ||
---|---|---|---|
60 Hz | 50Hz | ||
Coal | Bituminous coal / Sub-bituminous coal | ||
Power Generating Output | Gross | 460 MW | 540 MW |
Net | 410 MW | 480 MW | |
Gasifier method | Air blown and dry feed | ||
Gas clean-up method | Wet chemical absorption (Methyl Di-ethanol Amine (MDEA)) | ||
Gas Turbines | M501GAC×1 (1 on 1) |
M701F×1 (1 on 1) |
|
Net plant efficiency (LHV) | 48% |
- The power generation output, efficiency and other performance figures vary depending on the site conditions, coal properties and other factors.
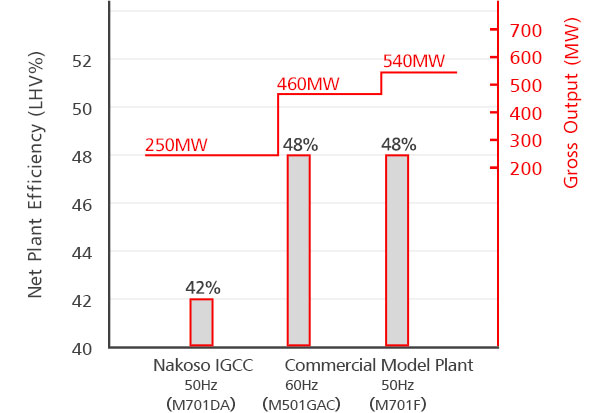
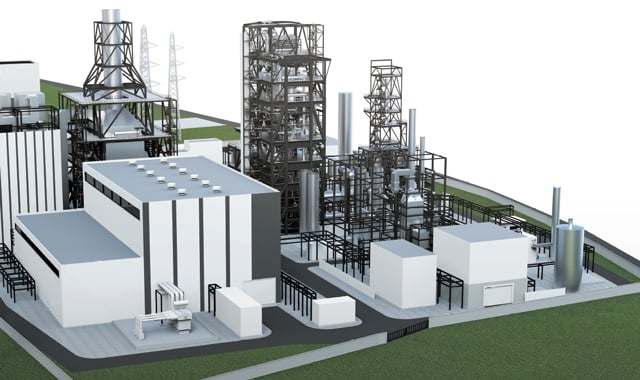
System Configuration
Oxygen-blown IGCC systems use oxygen for coal gasification.
First, coal is processed into coal gas in the gasifier, where oxygen is used as the gasification agent. Coal gas undergoes desulfurization and dedusting treatment in the gas clean-up unit to comply with the standards for gas turbine fuel and exhaust gas. The cleaned gas is supplied to the GTCC facility.
The GTCC facility burns the cleaned gas as fuel to turn the gas turbine for power generation. The heat of the exhaust gas is used to drive the heat recovery steam generator (HRSG) for heat exchange with water, which also generates steam for power generation from the steam turbine.
Placed downstream from the gasifier, the heat exchanger (or the syngas cooler (SGC)) cools the hot coal gas. At that time, steam is generated. It is merged into the HRSG and used for power generation with the steam turbine. It further increases power generation efficiency.
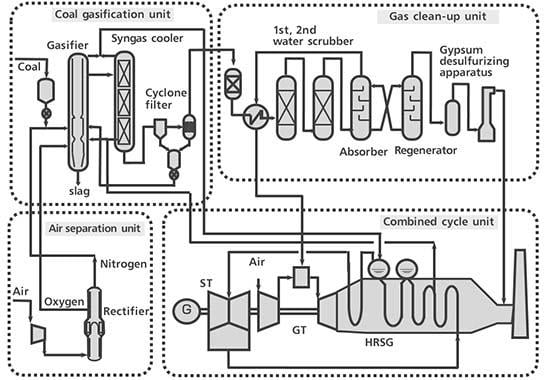
Features of the Oxygen-blown Gasifier
Oxygen-blown Gasifier
Our oxygen-blown gasifier is based on a single-chamber, two-stage, swirl-flow entrained-bed equipped with burners in the upper and lower stages of a cylindrical furnace. Appropriate oxygen/coal ratios can be allocated to the upper and lower stages in order to match the lower stage to the temperature required for melting ash and the upper stage to the conditions for an efficient gasification reaction according to the type of coal used. Moreover, a swirl flow can be generated in the gasifier to allow residence time for coal particles and to suppress the dispersion of char.
The measures described below were applied to the oxygen-blown gasifier: 1. The oxygen/coal ratios in the upper and lower stages were optimized, and the way of supplying seal gas was improved at the gasifier outlet (throat) to protect the throat from ash deposits (slagging). 2 The water-cooled piping on the gasifier wall was narrowed to step up cooling, and heat-resistant material was fusion-injected into the local high-temperature parts, in order to protect the gasifier walls. 3. The high-temperature gas flow (self-circulating flow) in the furnace and the slag flow-down promoting nozzle were used to insulate and heat the molten ash (slag) tapping hole, in order to cause slag to flow down stably. These measures solved the problems associated with the oxygen-blown gasifier.
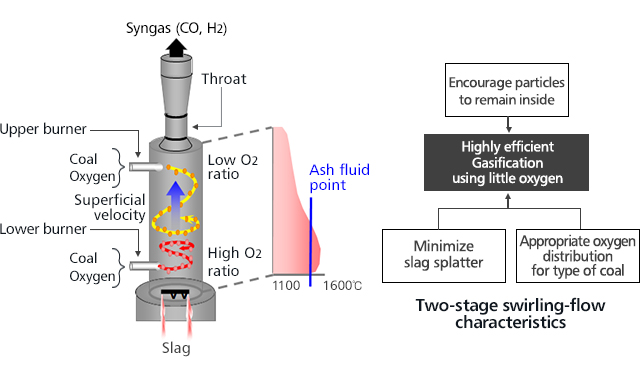
A Wide Range of Applicable Coal Types Suited for Replacing Conventional Pulverized Coal-fired Power Plants
The oxygen-blown gasifier is designed to gasify coal types in the applicable range for pulverized coal-fired power generation. It means that a wide range of coal types from sub-bituminous to bituminous coal are applicable and that it meets demand for replacing conventional pulverized coal-fired power plants.
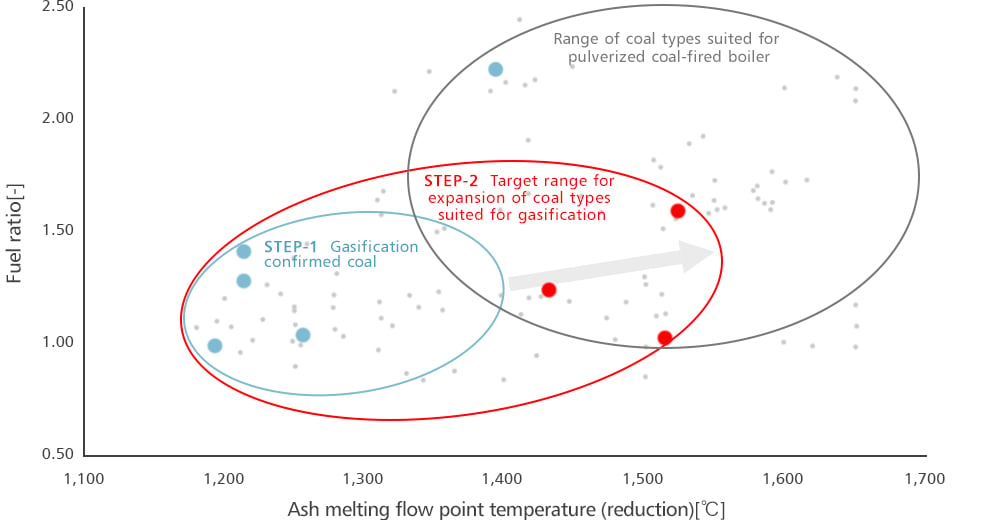
Net Thermal Efficiency
IGCC can increase net efficiency by applying high-efficiency technology based on a heated natural gas-fired gas turbine. Commercial oxygen-blown IGCC equipment based on a gas turbine has a net efficiency of about 46% (HHV), thereby saving CO2 emissions by about 10% from leading-edge pulverized coal-fired power plants. Oxygen-blown coal gasification captures CO2 from gas having a high CO2 content of about 40% under pressure ranging from 2.5 megapascals to 3.0 megapascals (pre-operation CO2 capture), so that the gas flow to be treated is lower than the CO2 content to be captured (post-operation CO2 capture) from the boiler exhaust gas. This makes it possible to use a smaller CO2 recovery unit and suppress the decline in net efficiency.
Effective Use of Ash
Ash discharged from IGCC has a lower unburned content than conventional pulverized coal-fired thermal power plants, and thus is recycled in road surface materials and others. The ash is also high in bulk density and has a volume ratio as small as 50%, thereby reducing the area needed to dispose of unused ash.
Comparison of oxygen-blown IGCC with conventional coal-fired power plant in ash volume, characteristics, etc.
IGCC | Pulverized coal-fired boiler (USC) | |
---|---|---|
Ash melted in gasifier and separated from syngas | Discharged with operation gas without melting ash | |
Bulk density | Approx. 1.4g/cm3(1.25 to 1.7g/cm3) | Approx. 0.7 g/cm3(0.5 to 0.8cm3) |
Volume ratio (%) |
![]() |
![]() |
Features |
|
|
Development History and Future Prospects for the Oxygen-blown Gasifier
Development History
Mitsubishi Power has been working to develop oxygen-blown gasification systems since the 1980s.
The company began with gasification element testing using a process development unit (PDU) with a coal feed rate of 1 ton per day, and then participated in the HYCOL project at 50 tons per day, which was a project on commission from the New Energy and Industrial Technology Development Organization (NEDO) and the HYCOL Research Association, and in the EAGLE project at 150 tons per day, a joint project with NEDO and Electric Power Development Co., Ltd. Thus, we have been taking steady steps to verify upscaling possibilities for a gasifier.
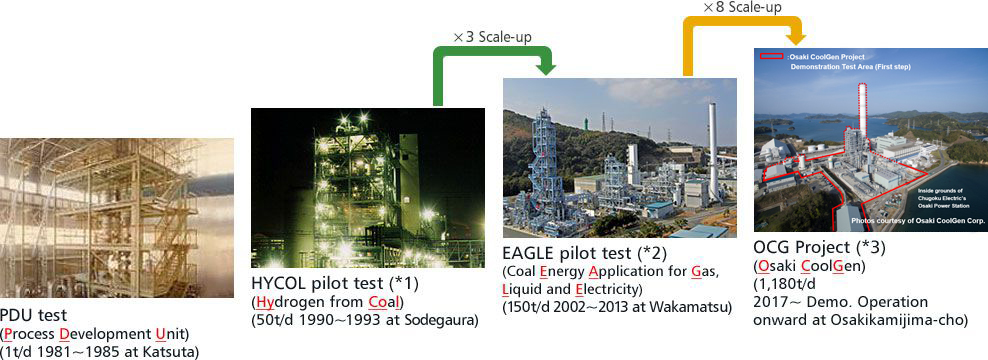
Implementation Bodies
- Hydrogen-from-Coal Process Research Association (HYCOL Association) (a project on commission from the New Energy and Industrial Technology Development Organization (NEDO))
- Electric Power Development Co., Ltd. (A joint research project with NEDO)
- Osaki CoolGen Corporation (a project sponsored by the Ministry of Economy, Trade and Industry (METI) and NEDO)
Eagle Project (A Program for Developing Technology for Manufacturing Multi-purpose Coal Gas)
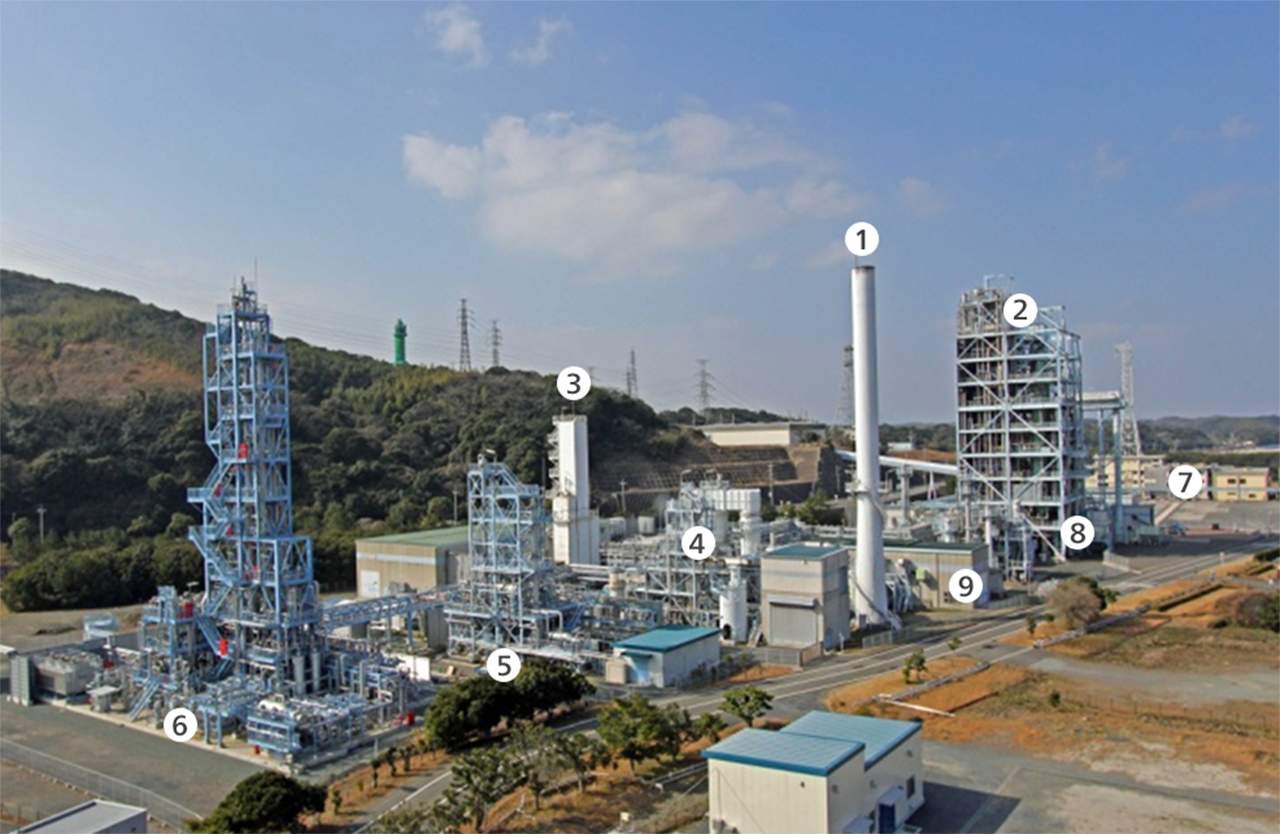
The EAGLE project is a joint research project between the New Energy and Industrial Technology Development Organization (NEDO) and Electric Power Development Co., Ltd.
- Stack
- Gasifier
- Air separation unit
- Sulfur recovery unit
- CO2 capture unit (chemical absorption)
- CO2 capture unit (sweet shift)
- Control room
- Gas clean-up unit
- Gas Turbines
EAGLE-STEP 1 (1998 to March 2007)
Mitsubishi Power delivered a gasifier, gas clean-up unit, gas turbine, generator, and other equipment, and also offered test-running support to Electric Power Development Co., Ltd. All initial development goals were achieved and the first-stage test run was finished in March 2007.
The table shows the basic specifications of the project and the test results.
EAGLE
Output | 8MW (Only GT) | |
---|---|---|
Coal consumption | Air dry basis | Approx. 150 metric tons per day |
Method | Gasifier | Oxygen blown and dry feed |
Gas clean-up | Wet (MDEA) and gypsum recovery | |
Gas Turbines | H-14 1260degC-class |
Test Results in the Project
- Gasification
Item | Target | Result | |
---|---|---|---|
Efficiency | Carbon gasification rate | More than 98% | More than 99% |
Cold gas efficiency | More than 78% | More than 82% | |
Reliability | Continuous operating time | More than 1,000 hours | 1,295 hours |
Operability | Coal types | 8 | 8 |
- Gas clean-up
Item | Target | Result | |
---|---|---|---|
Performance (actual O2) | Desulfurization performance Precision desulfurization outlet |
1 ppm or less | Less than 1 ppm |
Dust removal performance | 1 mg/mN3 or less | Less than 1 mg/mN3 |
EAGLE-STEP 2 (April 2007 to March 2010)
Mitsubishi Power retrofitted the existing gasifier and delivered a CO2 capture unit (chemical absorption).
Electric Power Development Co., Ltd. conducted a test run on a retrofitted gasifier until March 2010 to expand the range of applicable coal types and to verify reliability. In addition, in a world first, the company conducted a demonstrative test on CO2 capture (chemical absorption) from coal gas (Note).
- Gas treatment rate of 1,000 m3 per hour under normal conditions, CO2capture of about 24 metric tons per day
EAGLE-STEP 3 (April 2010 to June 2014)
Electric Power Development Co., Ltd. went on to conduct different tests and obtained design data applicable to the Osaki CoolGen project described below. The company completed 1,295 consecutive hours of operation and 14,511 cumulative hours of operation, thereby completing its 11-year test-run in November 2013.
Osaki CoolGen Project
With the knowledge obtained from the EAGLE project, the Osaki CoolGen project (Note1) is currently underway. This project consists of three steps. In the first step, an oxygen-blown integrated coal gasification combined cycle (oxygen-blown IGCC) demonstration was implemented from FY2016 to FY 2018. In the second step, a CO2 capture unit was added to the oxygen-blown IGCC, and demonstration of the oxygen-blown IGCC with CO2 capture started in FY2019. In the third step, a Solid Oxide Fuel Cell (SOFC) unit will be added to the IGCC with CO2 capture, and demonstration of the oxygen-blown IGFC (Note2) will start in FY2021. Mitsubishi Power is in charge of designing, manufacturing, installing, and test-running an oxygen-blown single-chamber, two-stage, swirl-flow entrained-bed gasifier with a coal feed rate of 1,180 t/day, 166-megawatt combined cycle power generation equipment, and electrical and control equipment for the first step. It is also in charge of engineering general management of the demonstrative plant and implementing regularly scheduled inspections of combined cycle power generation equipment. Mitsubishi Power is also in charge of designing, manufacturing, installing, and test-running a Solid Oxide Fuel Cell (SOFC) unit for the third step. The first step demonstration verifies the gasifier upscaling technology, establishment of gasifier operation control technology and the comprehensive oxygen-blown IGCC system. Setting a net efficiency target at 40.5% (HHV), among the highest in the world, the test resulted in 40.8% (HHV) net efficiency and successfully verified the high efficiency of the oxygen-blown IGCC. Consequently, net efficiency of about 46% (HHV) with commercial IGCC equipment is certainly possible, thereby accelerating the commercialization of efficient IGCC.
- 1This project is helped made possible by financial support from NEDO. It is implemented by Osaki CoolGen Corporation, jointly launched by Electric Power Development Co., Ltd. and the Chugoku Electric Power Co., Inc.
- 2Integrated Coal Gasification Fuel Cell Combined Cycle.
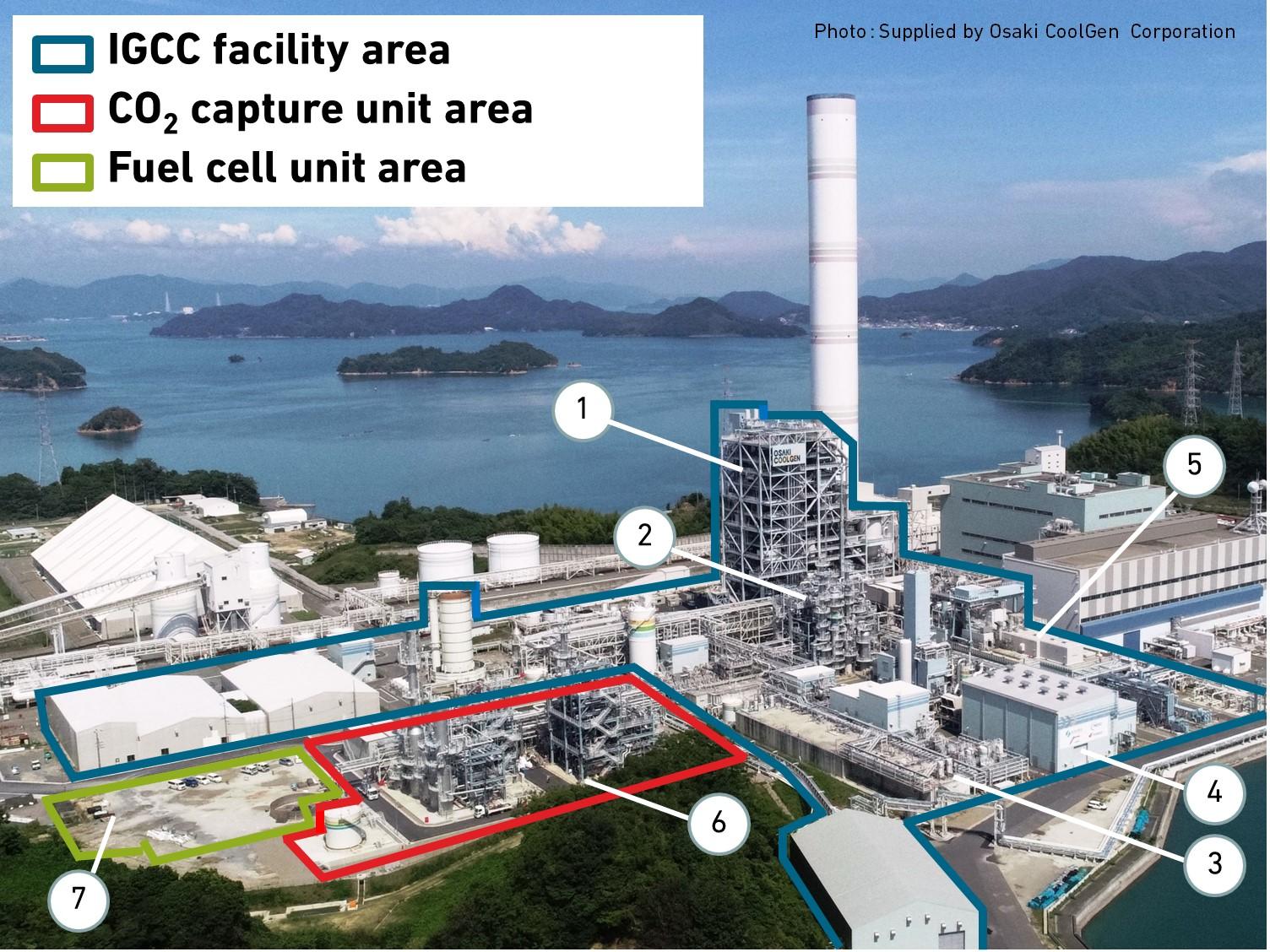
The Osaki CoolGen Project (FY2016- Demonstration)
- Coal gasification unit
- Gas clean-up unit
- Water treatment unit
- Air separation unit
- Combined cycle power plant
- CO2 capture unit
- Fuel cell unit
(Installation will be completed in FY2021)
Specifications of the Oxygen-Blown IGCC System and Major Schedule
OCG-PJ
Output | 166MW | ||
---|---|---|---|
Coal consumption | Air dry basis | Approx. 1,180 metric tons per day | |
Method | Gasifier | Oxygen blown and dry feed | |
Gas clean-up | Wet (MDEA) and gypsum recovery *1 | ||
Gas Turbines | H-100(100) 1300degC-class |
||
Target thermal efficiency | Net | 42.5% (LHV) | 40.5% (HHV) *2 |
Target thermal efficiency (targets) |
SOx emission concentration | 8 ppm *2 | 16% O2 basis |
NOx emission concentration | 5 ppm *2 | ||
Dust emission concentration | 3 mg/m3N *2 |
- *1 Gas clean-up system is out of Mitsubishi Power Scope
- *2 Achieved all target items of demonstration test
Project schedule
Start of construction | March 2013 |
---|---|
Receipt of electricity | November 2015 |
Initial firing of the gasifier | June 2016 |
Start of verification tests | March 2017 |
Schedule and Details of Verification Tests with the Oxygen-blown IGCC System
Source: Osaki CoolGen Corp.: Company brochure
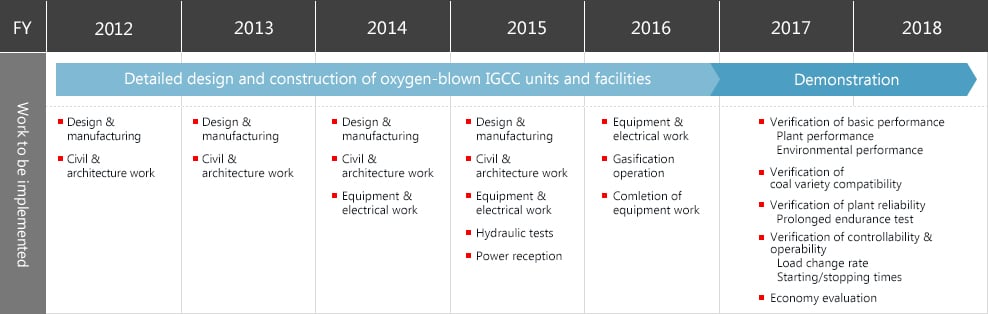
Detailed Design and Construction of the Oxygen-Blown IGCC
Osaki CoolGen Project Schedule
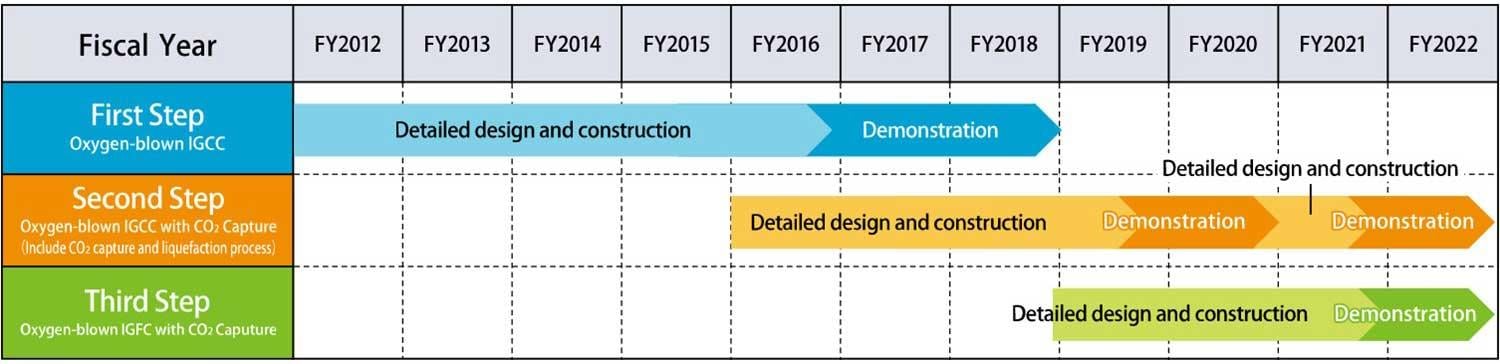
Commercialization
The oxygen-blown gasifier produces high calorie coal gas and is suited to multi-purpose use. In parallel with the implementation of the Osaki CoolGen project, Mitsubishi Power will be working towards commercializing gasifiers for chemical materials.
With gasifiers for chemical materials, we will verify these technologies described below with a view to cutting construction costs and improving efficiency: 1. Enhanced cold gas efficiency based on gasification into circulating CO2 gas, 2. Cooling and humidification of generated gas by direct quench, and 3. Cold gas efficiency improved by gasification with steam addition . Among others advantages, direct quench is expected to considerably reduce construction costs because it eliminates the heat recovery boiler. We are also undertaking development to apply it to a pilot project of increasing interest recently, in which hydrogen is produced from brown coal for hydrogen chains.
- Reference
Nagasaki and Kameyama: "Latest Technologies for Coal-Fired Thermal Power Generation: Integrated Coal Gasification Combined Cycle (Oxygen-Blown Technology)" in The Thermal and Nuclear Power, 65 [10], pp. 69-73 (2014)
Products
- GTCC
- Steam Power
- IGCC
- Geothermal
-
Gas Turbines
- Product Lineup
- Comparative Performance
-
Technical Information
- Gas Turbines for Mechanical Drive Applications
- Cutting-Edge Elemental Technology Producing 1600°C Class J Gas Turbines
- Development of High-Efficiency Gas Turbine Applying 1600°C Class J Technology
- Combustor Technologies Supporting Stable Operation
- Overview and Verification Status of T-Point 2 Demonstration Facility
- Comprehensive Efforts from Development to Manufacturing
- Summary of Orders
- Development History
- Product Selection Assistant (Middle & small Class)
- Aero-derivative Gas Turbines
- Steam Turbines
- Boilers
- Air Quality Control Systems (AQCS)
- Generators
-
Control Systems
- What is DIASYS?
- DIASYS Netmation
-
DIASYS Optional Products
- IR-S Infrared Flame Detector
- Net IR-S Infrared Flame Detector
- Rail Mounting Net IR-S
- Boiler Tube Leak Detector
- Shaft Vibration Analyzer
- Simulator
- Advanced Combustion Pressure Fluctuation Monitoring System (A-CPFM) / Combustion Pressure Fluctuation Monitoring System (CPFM)
- Multi-Coal Fired Boiler Optimum Control
- FXtoLS Adapter
- Fuel Cells
- Additive Manufacturing
- Catalogue
- HIACS Series
- Technical Report