Fans and Blowers
Overview
Mitsubishi Power fans and blowers achieve high reliability and excellent operational performance backed up by extensive experience and the latest design and manufacturing technologies.
Mitsubishi Power fans are used in a wide range of fields also to customers other than its own, from power plants to exhaust desulfurization equipment, blast furnaces, sintering furnaces and tunnel ventilation.
We achieve high levels of reliability through experience based on a long track record and designs based on the latest research data. Mitsubishi Power has gained world renown for its technological capabilities and reliability.
We have also established a well-prepared service structure to respond to customer requests.
In addition, Mitsubishi Power maintains plant operating facilities where it can run actual fans, as well as balance testing equipment. This ensures that we provide products with verified performance and quality.
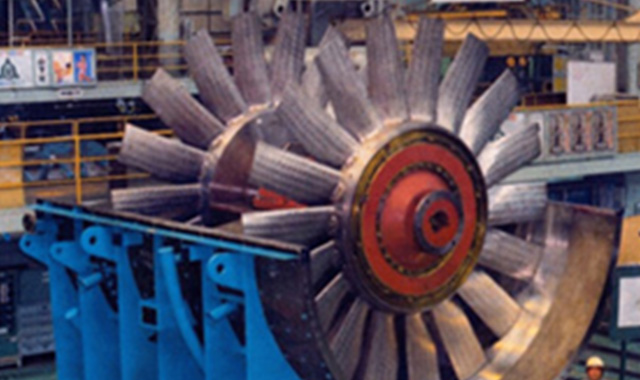
World-class Axial Fans with Variable Rotor Blade Pitch
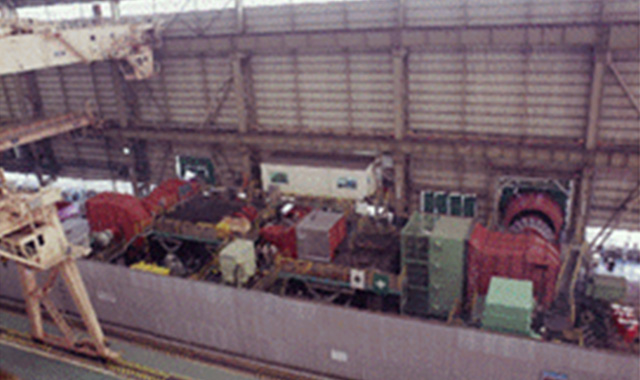
Plant Operating Facilities
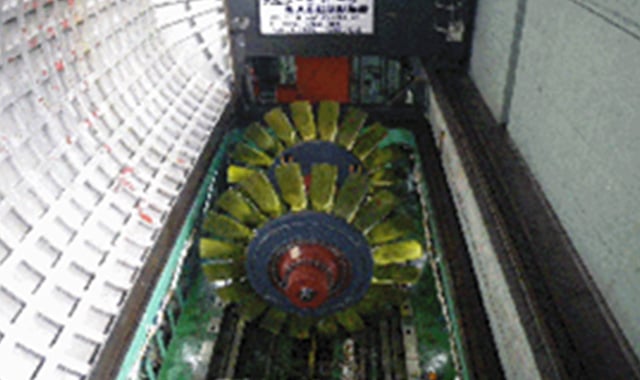
Balance Testing Equipment
Track Record of Deliveries
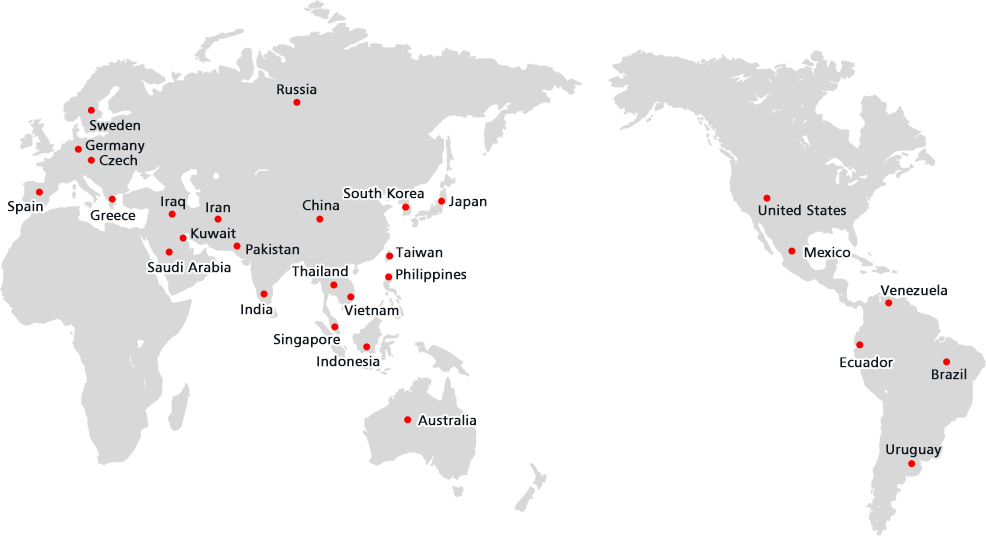
Axial fans with variable rotor blades | At least 500 units |
---|---|
Centrifugal fans | At least 1,500 units |
Multistage axial blowers and compressors | At least 150 units |
History
1945 | Commenced research and development into axial-flow equipment |
---|---|
1954 | Manufactured gas turbine compressor for Transport Ministry vessel Hokuto Maru (First gas turbine unit from Mitsubishi Heavy Industries) |
1958 | Manufactured and delivered axial-flow compressor for blast furnace (first blast furnace air blower unit produced by Mitsubishi Heavy Industries)
![]() |
1965 | Manufactured axial fan with variable rotor blades for commercial boiler (First axial fan with variable rotor blades for boilers produced by Mitsubishi Heavy Industries) |
1974 | Began production of centrifugal fans |
1975 | Began research, development and production of centrifugal compressors |
1976 | Established CE-MHI Fan Co. with US-based CE (up to 1988) (Company manufacturing and selling axial-flow blowers for power plant boilers) |
1979 | Began licensing variable rotor blade axial fan technologies to Spanish company DURO-FELGUERA (up to 1987) |
1979 | Developed Japan' s first submarine masker compressor Developed gas extraction compressor for geothermal power plants |
1985 | Developed Mitsubishi Heavy Industries' first steam compressor |
1988 | Began licensing variable rotor blade axial fan technology to Chinese-based Wuhan Blower Co., Ltd. |
1991 |
Manufactured wind tunnel axial-flow compressors (blowers) for US Department of Defense ![]() |
1993 | Manufactured pressurized wind tunnel axial-flow compressors (blowers) for US-based NASA |
2000 | Manufactured flue gas desulfurization equipment for large-scale thermal power plant (highly corrosive environment) and FRP variable rotor blade axial fan
![]() |
2003 | Manufactured helium axial-flow compressor for atomic energy agency |
2005 |
Manufactured recirculating blowers for fuel cell (solid oxide fuel cell - SOFC) power generating equipment ![]() |
2014 | Manufactured 15MW class variable rotor blade axial fans
![]() |
Research and Development
Mitsubishi Power is actively pursuing the design and development of turbo machines for new power generating systems (thermal, nuclear and fuel cell-based).
We are also consistently focused on realizing further reliability gains and improved efficiency to meet the needs of customers using our existing products. The following are some examples of our research and development efforts.
Development of FRP Rotor Blades
Fiber-reinforced plastic (FRP) rotor blades are made from a composite material where thermoset plastic is reinforced with fiber glass. These rotor blades offer the following advantages over metallic blades.
- Will not rust or decay
- Lightweight (Roughly 1/4th the weight of carbon steel)
- High specific strength (Around three times that of carbon steel)
- Excellent vibration absorption and shock absorption properties
To date, FRP rotor blades have only been developed for commercial use in jet engine compressor blades for aircrafts (carbon fiber-reinforced type), cooling tower fans and wind turbines (fiber glass-reinforced type), but based on the rotor blades used in wind turbines, Mitsubishi Power has pursued innovation in structure, materials and forming methods to complete the development of FRP rotor blades that boast high strength and reliability.
Services and Proposals for Improved Energy Savings
Mitsubishi Power has established a reliable service structure to ensure that delivered fans and blowers arrive in a healthy state and demonstrate adequate performance, and is committed to responding to customer requests. We help customers boost productivity and save more energy by employing the latest technologies to increase the capacity of fans and blowers that were delivered in the past.
Example of Energy-saving Improvements for Existing Fans
Switching Existing Centrifugal Fans to Axial Flow Fans
- By replacing existing centrifugal fans with variable rotor blade axial fans that feature higher efficiency under partial loading, Mitsubishi Power contributes to energy saving measures at plants.
- Improvements to partial loading efficiency can be expected to have energy-saving effects of up to 40%.
Modifications to Multistage Axial Compressors (Blowers)
- Mitsubishi Power has a track record of making modifications to compressors in line with customer needs, such as switching between rotating and stationary blades in a compressor to cater to increases or decreases in plant production.
Products
- GTCC
- Steam Power
- IGCC
- Geothermal
-
Gas Turbines
- Product Lineup
- Comparative Performance
-
Technical Information
- Gas Turbines for Mechanical Drive Applications
- Cutting-Edge Elemental Technology Producing 1600°C Class J Gas Turbines
- Development of High-Efficiency Gas Turbine Applying 1600°C Class J Technology
- Combustor Technologies Supporting Stable Operation
- Overview and Verification Status of T-Point 2 Demonstration Facility
- Comprehensive Efforts from Development to Manufacturing
- Summary of Orders
- Development History
- Product Selection Assistant (Middle & small Class)
- Aero-derivative Gas Turbines
- Steam Turbines
- Boilers
- Air Quality Control Systems (AQCS)
- Generators
-
Control Systems
- What is DIASYS?
- DIASYS Netmation
-
DIASYS Optional Products
- IR-S Infrared Flame Detector
- Net IR-S Infrared Flame Detector
- Rail Mounting Net IR-S
- Boiler Tube Leak Detector
- Shaft Vibration Analyzer
- Simulator
- Advanced Combustion Pressure Fluctuation Monitoring System (A-CPFM) / Combustion Pressure Fluctuation Monitoring System (CPFM)
- Multi-Coal Fired Boiler Optimum Control
- FXtoLS Adapter
- Fuel Cells
- Additive Manufacturing
- Catalogue
- HIACS Series
- Technical Report