Multi-Coal Fired Boiler Optimum Control
Overview
Multi-coal fired boiler optimum control is an algorithm that allows the optimum control for multiple types of coal. Mitsubishi Power's unique method is used for comprehensively checking the coal characteristics and status, and the boiler combustion status based on the heat balance of each heating surface of boiler.
This system is offered using components of DIASYS Netmation.
-
Related Links
Features
An Extensive Delivery Track Record
Since the first delivery in 1997, a large number of Multi-Coal Fired Boiler Optimum Control systems have been delivered for supercritical-pressure variable-pressure once-through boilers. Parts of this system have also been delivered for drum type boiler plants.
Changing Parameters is not Necessary When Coal Types are Switched
The control parameters of the boiler are automatically set based on estimates of the state of the heating surfaces of the boiler. Consequently, changing parameters whenever a different coal type or coal type group is used is no longer necessary.
Multi-Coal Fired Boiler Optimum Control can automatically set the control parameters for a boiler even when blended coal is used.
Shorter Adjustment Period When a New Type of Coal is Used
Even when a new type of coal is to be used, if it can be burned mechanically by adjusting combustion, Multi-Coal Fired Boiler Optimum Control can reduce or even eliminate the APC adjustment period.
Functions
Multi-Coal Fired Boiler Optimum Control offers the following functions.
Characteristics Change by Coal Type (Heat Absorption Characteristics, Generated Heat)
Estimation of the Heat Absorption Distribution (heat absorption index)
If the heat absorbed by each heating surface is estimated, the control parameters can be adjusted for the heat absorbed by the boiler. Consequently, compared to the case where the control parameters are switched based on a coal type group, more precise control parameters can be fed.
Adjustment for Generated Heat
If the heat absorbed by each heating surface is estimated, the heat input from the coal and air and the heat output to the gas at the boiler exit can be calculated online. Based on the heat input and output, the generated heat can be estimated, and the fuel parameters can be adjusted in a precise manner.
Estimation of the Moisture Content of the Coal
The moisture content of the coal can be estimated from the heat balance in the mill. Using this estimation along with the mill current and roller lift, you can get the characteristics of the columnar coal and automatically set the parameters related to the mill, such as the mill exit temperature, the rotation speed of the mill rotating classifier, and the oil pressure of the mill pressure device.
Estimation of the Mill Load Ratio
By using model calculations based on a mill model, the hard grove index (HGI) can be estimated. By using this estimation along with the estimate of the moisture content of the coal, you can adjust the reference capacity of the mill, and you can estimate the mill load ratio from the actual amount of supplied coal.
Boiler Characteristics Change Over Time
Estimation of the Cleanness of The Heating Surfaces
If the heat absorbed by each heating surface is estimated, the thermal conductivity can be calculated online. As the combustion in the boiler continues, the thermal conductivity decreases. Optimum timing of activating soot blowers should be based on time and also on the thermal conductivity as a good indicator.
System Configuration
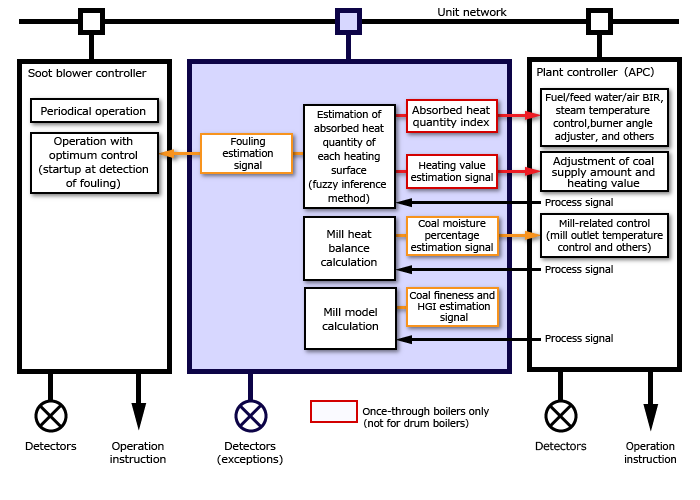
Real-time Calculation Based on Fuzzy Logic
The state of heating surfaces can be estimated based on fuzzy logic. The effect of a coal type can be calculated with high precision in real time from the absorbed heat.
Constructed from Software Logic
The whole Multi-Coal Fired Boiler Optimum Control can be constructed with DIASYS software logic using the Interpreter DDC Oriented Language (IDOL).
Easy Extension from a Preexisting System
Except for a few sensors(Note), all sensors necessary for Multi-Coal Fired Boiler Optimum Control are already built into a plant control unit (APC).
- RH spray water flow, primary RH entrance steam flow and denitration entrance gas temperature
Specifications
Hardware Specifications
The specifications of the hardware necessary for Multi-Coal Fired Boiler Optimum Control are as follows.
Models | DIASYS Netmation (duplexed CPU, single PIO system) |
|
---|---|---|
Construction | P-33 (dust-proof, water-proof specifications) | |
Environmental conditions | 0 - 55℃, RH up to 90% | |
Number of boards / dimensions | 1 board / 800mm(W) x 800mm(D) x 2,300mm(H) | |
Insulation resistance | 500VDC / 5MΩ or greater (Power supply-FG or I/O modules-FG) |
|
Withstand voltage | Power supply-FG | 1a |
Digital I/O terminal-FG | 1a | |
Analog I/O terminal-FG | 1b | |
Coating (external, internal, channel base) | Munsell 5Y7/1 (half gloss) | |
Other | Dedicated maintenance tool and gateway device
|
Software Specifications
The specifications of the software necessary for Multi-Coal Fired Boiler Optimum Control are as follows.
Variable-pressure once-through boiler | Constant-pressure once-through boiler | Drum boiler | |
---|---|---|---|
Descriptive language | IDOL | ||
Operating speed | 100msec | ||
Number of control loops | Depends on the equipped features and existing system. | ||
Absorbed heat quantity index | Available (load change test with at least 3 coal types is required) |
Not available | |
Heating value adjustment | ○ | Not available | |
Heating surface fouling | ○ | ||
Moisture percentage in coal | Detected (estimated for each mill) |
||
Mill load factor | Detected (estimated for each mill) |
Products
- GTCC
- Steam Power
- IGCC
- Geothermal
-
Gas Turbines
- Product Lineup
- Comparative Performance
-
Technical Information
- Gas Turbines for Mechanical Drive Applications
- Cutting-Edge Elemental Technology Producing 1600°C Class J Gas Turbines
- Development of High-Efficiency Gas Turbine Applying 1600°C Class J Technology
- Combustor Technologies Supporting Stable Operation
- Overview and Verification Status of T-Point 2 Demonstration Facility
- Comprehensive Efforts from Development to Manufacturing
- Summary of Orders
- Development History
- Product Selection Assistant (Middle & small Class)
- Aero-derivative Gas Turbines
- Steam Turbines
- Boilers
- Air Quality Control Systems (AQCS)
- Generators
-
Control Systems
- What is DIASYS?
- DIASYS Netmation
-
DIASYS Optional Products
- IR-S Infrared Flame Detector
- Net IR-S Infrared Flame Detector
- Rail Mounting Net IR-S
- Boiler Tube Leak Detector
- Shaft Vibration Analyzer
- Simulator
- Advanced Combustion Pressure Fluctuation Monitoring System (A-CPFM) / Combustion Pressure Fluctuation Monitoring System (CPFM)
- Multi-Coal Fired Boiler Optimum Control
- FXtoLS Adapter
- Fuel Cells
- Additive Manufacturing
- Catalogue
- HIACS Series
- Technical Report