Boiler Tube Leak Detector
Overview
A boiler tube leak detector can discover high-pressure steam or water leaks caused by rupture of a boiler furnace water wall, super-heater, or reheat combustor at an early stage to keep damage to the customer's boiler to a minimum.
Features
Detection of Tiny Leaks
A boiler tube leak detector continuously monitors for tube leaks and can immediately detect leaks that cannot be heard on-site by patrol personnel.
Reducing Boiler Downtime and Repair Expense
By keeping damage to the tube caused by ruptures to a minimum, you can reduce boiler downtime and repair expense.
Enabling Appropriate Decisions on Downtime
By monitoring the trend of the leak when it occurs, you can make an appropriate decision about the downtime of the unit.
Support for a Variety of Fuel Boilers and Easy Installation
Various types of fuel boilers are supported, and installing a detector to a boiler is easy.
The guidelines for the number of sensors to be installed are as follows (Note).
- Consultation may be required to decide the exact number.
Uses | Qty |
---|---|
Electric utility | About 20 - 30 |
Industry | About 10 or less |
Principle
Since the frequency of the vibration generated by leak is different from that of the vibration during normal operation (background vibration), the vibration of the boiler furnace wall is constantly monitored and if the vibration level in a certain frequency band exceeds the threshold value, the leak is judged to have occurred.
Theoretical leak detection capability(Note1) is as follows.
The level of normal boiler vibration noise depends on the structure of the boiler and the positioning of the sensors. The leak level depends on the direction or angle of the ejected spray as well as the spray strikes anything or not.
Pressure | 10.19kg/cm²(1MPa) |
---|---|
Nozzle Diameter | 5.0mm |
Distance to Sensor | About 10m |
- 1Evaluation result of 500MW class boiler
System Configuration
Basic System Configuration
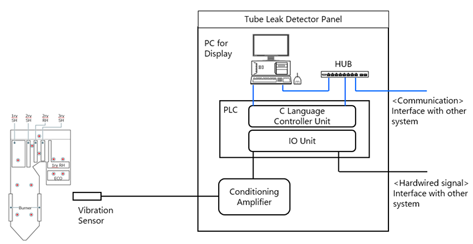
The vibration type tube leak detector consists of "acceleration sensor" mounted on the wall of a boiler furnace to detect vibration caused by leakage from a broken hole, and "PLC system" to monitor and display the existence of leakage by frequency analysis of the vibration electrical signal obtained from the acceleration sensor.
Tube Leak Detector Panel
The system can input and process signals of up to 32 sensors per a single panel. The vibration value of each sensor is color-coded according to the level and displayed on the monitor screen of the display PC installed in the panel, so that the sensor close to the place where the leak occurred can be easily identified. In addition, the tube leak detector panel can interface with other devices using hard signals or communication signal.
Sensors
Each sensor consists of "Waveguide" and "Vibration sensor". The arrangement and number of sensors vary depending on the size of the boiler, the arrangement of heat transfer tubes, or where you want to detect them. Since there is no need to install an opening in the furnace wall, it can be installed with simple construction.
Specifications
Sensor
The specification of Vibration sensor are as follows.
Item | Specification |
---|---|
Vibration sensor | Accelerometer |
Operation temperature range | -50 ~ 121 degC |
Waveguide | SUS304, SS400, SA387-22-1 |
Signal cable | 3C2V |
Tube Leak Detector Panel
The specification of Tube leak detector panel are as follows.
Description | Specification | |
---|---|---|
Panel | 19 inch system rack (double side door) | |
Dimensions | 1800mm(H) x 700mm (W) x 800mm(D)(Note1) | |
Operating temperature range | 5 ~ 40degC | |
Conditioning amplifier unit | Input Channels | 32CH (max.) (Note1) |
Output Channels | 32CH (max.) (Note1) | |
Power Supply | AC 100 ~ 240V (50/60Hz) | |
C language controller unit (MELSEC iQ-R Series) |
Input Channels | 32CH (max.) (Note1) |
Frequency Range | DC ~60Hz (max.) | |
Power Supply | AC100 ~ 240V (50/60Hz) | |
Display PC (Note2) | CPU | Pentium processor G5400 |
OS | Windows | |
Power Supply | AC100 ~ 240V (50/60Hz) | |
LCD | 19 inches (Color) |
- 1Dimensions and Maximum number of channel to be stored in a single panel. Depending on the number of measurement points, it will be multi-panel to increase the maximum number of channels.
- 2The specification of PC may change depending on the market.
Example of leak detection
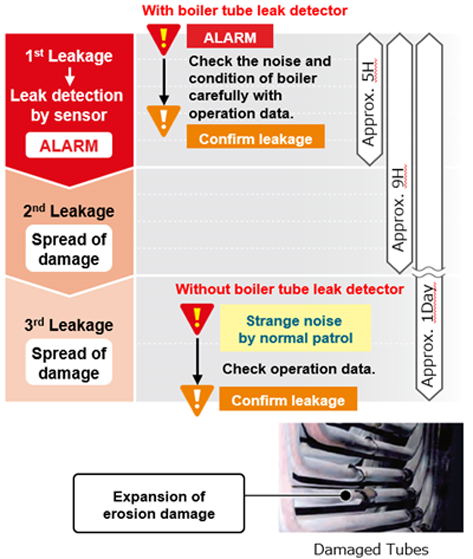
Products
- GTCC
- Steam Power
- IGCC
- Geothermal
-
Gas Turbines
- Product Lineup
- Comparative Performance
-
Technical Information
- Gas Turbines for Mechanical Drive Applications
- Cutting-Edge Elemental Technology Producing 1600°C Class J Gas Turbines
- Development of High-Efficiency Gas Turbine Applying 1600°C Class J Technology
- Combustor Technologies Supporting Stable Operation
- Overview and Verification Status of T-Point 2 Demonstration Facility
- Comprehensive Efforts from Development to Manufacturing
- Summary of Orders
- Development History
- Product Selection Assistant (Middle & small Class)
- Aero-derivative Gas Turbines
- Steam Turbines
- Boilers
- Air Quality Control Systems (AQCS)
- Generators
-
Control Systems
- What is DIASYS?
- DIASYS Netmation
-
DIASYS Optional Products
- IR-S Infrared Flame Detector
- Net IR-S Infrared Flame Detector
- Rail Mounting Net IR-S
- Boiler Tube Leak Detector
- Shaft Vibration Analyzer
- Simulator
- Advanced Combustion Pressure Fluctuation Monitoring System (A-CPFM) / Combustion Pressure Fluctuation Monitoring System (CPFM)
- Multi-Coal Fired Boiler Optimum Control
- FXtoLS Adapter
- Fuel Cells
- Additive Manufacturing
- Catalogue
- HIACS Series
- Technical Report