M501D Series
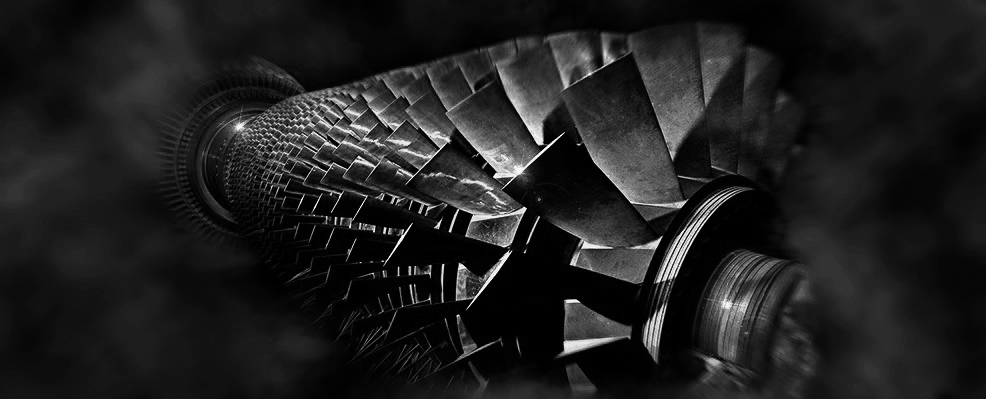
-
Standalone Gas Turbine Output
110 MW class
-
Combined Cycle Output
170 MW class / 340 MW class / 510 MW class
-
Fuel Diversification
Compatible with blast furnace gas (BFG)
Gas turbines for 60 Hz power generation matched with diversification of fuels
In 1984, a 1,090 MW heat recovery combined cycle power plant, which was powered by six 701D gas turbines, began commercial operation. This is the dawn of the current era of combined cycle power generation. The DA series incorporates the F-class technology into the D Series to improve overall performance.
Overall Design
The gas turbine unit is based on the basic structure adopted in the early 1970s that has accumulated a track record of at least 50 years. Its main features are as follows:
- A compressor shaft end drive reduces the effect of thermal expansion on alignment
- A rotor with simple single-shaft two-bearing support
- A rotor structure has bolt-connected discs with the torque pins in the compressor section and CURVIC couplings in the turbine section to ensure stable torque transmission
- An axial flow exhaust structure advantageous in combined cycle plant layouts
- Horizontally split casings that facilitate field removal of the blades with the rotor in place
Compressor
The DA Series incorporates a high efficiency compressor with a proven track record. Stationary vanes at backward stages are supported by blade rings to minimize the tip clearance of rotating blades.
Variable inlet guide vanes ensure operational stability at the start-up and enhanced performance at partial load in combined cycle operation.
Combustor
Mitsubishi Power introduced the world' s first commercial dry low NOx combustors to the D Series gas turbines in 1984. A premixing low NOx combustor is composed of one pilot burner and eight main burners that surround it. The combustor has an air bypass mechanism that enables fuel-air ratio regulation in the combustion region.
Turbine
In response to the increase in the turbine inlet temperature, stationary vanes at the first three stages and rotor blades at the first two stages are air-cooled. The rotating blades at the fourth stage is equipped with a Z-shaped shroud to enhance the vibration resistance strength of the blades.
Stationary vanes are supported by blade rings that are independent at individual stages to prevent the turbine casings from being affected by thermal expansion.
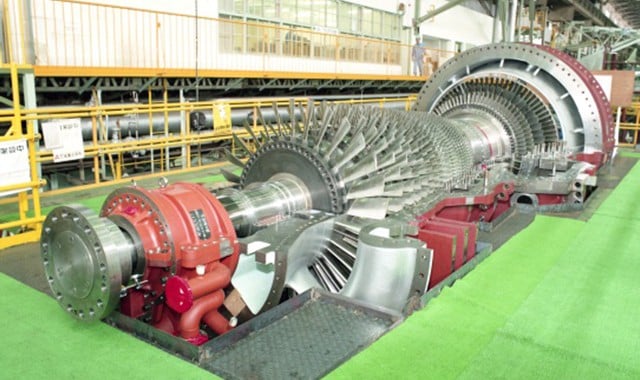
Configuration
M501DA | ||
---|---|---|
Compressor | Number of Stages | 19 |
Combustor | Number of Cans | 14 |
Cooling Method | Air Cooled | |
Turbine | Number of Stages | 4 |
Rotor | Number of Rotors | 1 |
Output Shaft | Cold End | |
Rated Speed | 3,600 rpm | |
Gas Turbine | Approx. L × W × H | 11.4 × 4.5 × 4.8 m |
Approx. Weight | 190 ton |
Simple Cycle Performance
M501DA | ||
---|---|---|
Frequency | 60 Hz | |
ISO Base Rating | 113.95 MW | |
Efficiency | 34.9 %LHV | |
LHV Heat Rate | 10,320 kJ/kWh | |
9,780 Btu/kWh | ||
Exhaust Flow | 354 kg/s | |
780 lb/s | ||
Exhaust Temperature | 543 °C | |
1,009°F | ||
Exhaust Emission | NOx | 25 ppm@15%O2 |
CO | 30 ppm@15%O2 | |
Turn Down Load | 75 % | |
Ramp Rate | 7 MW/min | |
Starting Time | 30 minutes |
Combined Cycle Performance
M501DA | ||
---|---|---|
1 on 1 | Plant Output | 167.4 MW |
Plant Efficiency | 51.4 %LHV | |
2 on 1 | Plant Output | 336.2 MW |
Plant Efficiency | 51.6 %LHV | |
Starting Time | 70 minutes |
Performance Correction Curves
-
Effects of Compressor Inlet Temperature on Gas Turbine Performance (Typical)
-
Effects of Barometric Pressure on Gas Turbine Performance (Typical)
Typical Plant Layout - 1 on 1 configuration, single-shaft
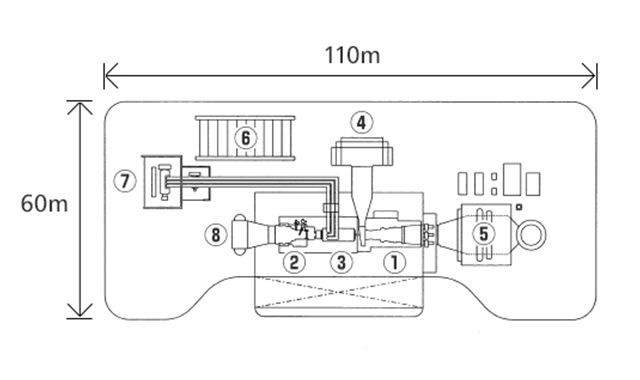
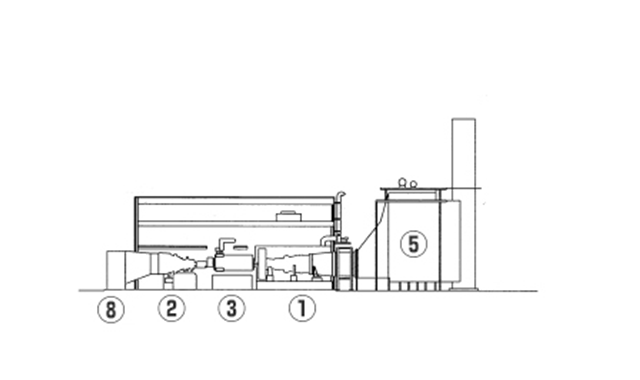
- Gas Turbines
- Steam Turbines
- Generators
- Inlet Air Filter
- Heat Recovery Steam Generator (HRSG)
- Electrical / Control Package
- Main Transformer
- Condenser
Typical Plant Layout - 2 on 1 configuration
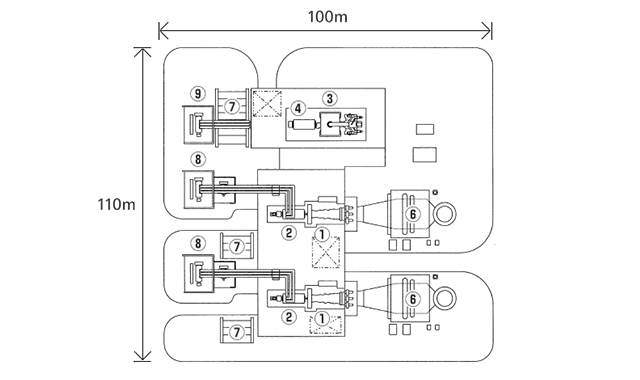
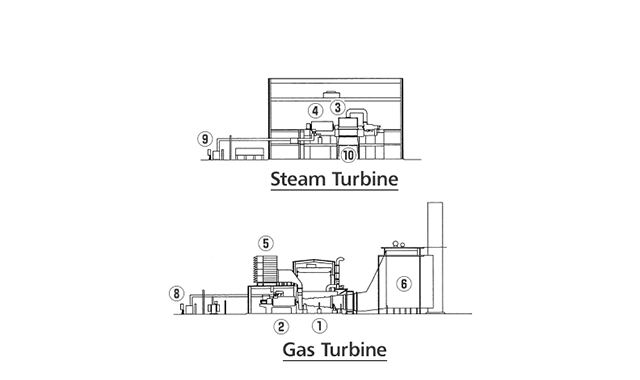
- Gas Turbines
- GT Generator
- Steam Turbines
- ST Generator
- Inlet Air Filter
- Heat Recovery Steam Generator (HRSG)
- Electrical / Control Package
- GT Main Transformer
- ST Main Transformer
- Condenser
Delivery Records Example
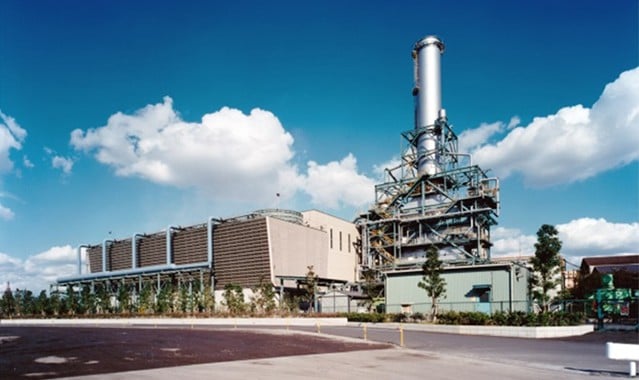
Funamachi Power Station, Nakayama Kyodo Hatsuden Co., Ltd. (Japan)
149 MW, 1 x M501DA
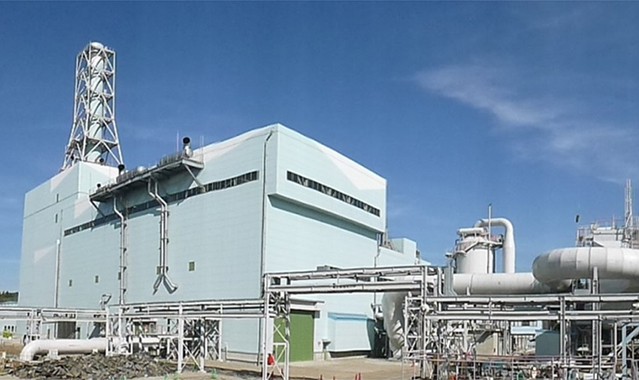
Wakayama Kyodo Power Station Unit 1, Wakayama Kyoto Power Co., Inc. (Japan)
147 MW, 1 x M501DA
Order Results Example
Number of units x Series | Year of start of operation | Plant specifications | |
---|---|---|---|
POSCO Power Corp. (Korea) | 4 × M501DA | 2010-2014 | Blast furnace gas-fired combined cycle |
Wakayama Kyodo Power Station Unit 1, Wakayama Kyoto Power Co., Inc. (Japan) | 1 × M501DA | 2014 | Blast furnace gas-fired combined cycle |
Shinko Kakogawa Power Station Units 1 and 2, Kobe Steel, Ltd. (Japan) | 2 × M501DA | 2011, 2015 | Blast furnace gas-fired combined cycle |
Oita Co-operative Thermal Power Station Unit 3, Oita Co-operative Thermal Power Co., Inc. (Japan) | 1 × M501DA | 2015 | Blast furnace gas-fired combined cycle |
Products
- GTCC
- Steam Power
- IGCC
- Geothermal
-
Gas Turbines
- Product Lineup
- Comparative Performance
-
Technical Information
- Gas Turbines for Mechanical Drive Applications
- Cutting-Edge Elemental Technology Producing 1600°C Class J Gas Turbines
- Development of High-Efficiency Gas Turbine Applying 1600°C Class J Technology
- Combustor Technologies Supporting Stable Operation
- Overview and Verification Status of T-Point 2 Demonstration Facility
- Comprehensive Efforts from Development to Manufacturing
- Summary of Orders
- Development History
- Product Selection Assistant (Middle & small Class)
- Aero-derivative Gas Turbines
- Steam Turbines
- Boilers
- Air Quality Control Systems (AQCS)
- Generators
-
Control Systems
- What is DIASYS?
- DIASYS Netmation
-
DIASYS Optional Products
- IR-S Infrared Flame Detector
- Net IR-S Infrared Flame Detector
- Rail Mounting Net IR-S
- Boiler Tube Leak Detector
- Shaft Vibration Analyzer
- Simulator
- Advanced Combustion Pressure Fluctuation Monitoring System (A-CPFM) / Combustion Pressure Fluctuation Monitoring System (CPFM)
- Multi-Coal Fired Boiler Optimum Control
- FXtoLS Adapter
- Fuel Cells
- Additive Manufacturing
- Catalogue
- HIACS Series
- Technical Report